Preparation method of ceramic core easy to release
A technology of ceramic core and graphite core, applied in the direction of core, casting molding equipment, casting mold, etc., can solve the problems of increasing the production cost of castings, long core core removal time, casting failure, etc., to reduce core core removal difficulty and simple method. , the effect of reducing production costs
- Summary
- Abstract
- Description
- Claims
- Application Information
AI Technical Summary
Problems solved by technology
Method used
Examples
Embodiment 1
[0023] (1) Preparation of graphite core
[0024] a. Slurry preparation
[0025] Weighing by weight: spherical graphite 325 mesh 20%, spherical graphite 500 mesh 70%, spherical graphite 800 mesh 10%. The above-mentioned spherical graphite powder was mixed evenly and then put into an oven and dried at 120° C. for 12 hours. Weighing by weight: 70% of the dried spherical graphite powder, 2% of quartz glass fiber, and 28% of ceramic core plasticizer. Raise the temperature of the mixer to 100°C, add ceramic core plasticizer, and after it is completely melted, add the dried graphite into the mixer in proportion, stir for 4 hours, and take it out to obtain the graphite core slurry.
[0026] b. Forming
[0027] Put the prepared graphite core slurry into a ceramic core injection molding machine to prepare a graphite core green body.
[0028] c. Graphite core firing
[0029] The graphite core green body was embedded in 200-mesh alumina powder and fired at a firing temperature of 450...
Embodiment 2
[0038] (1) Preparation of graphite core
[0039] a. Slurry preparation
[0040] Weighing by weight: spherical graphite 325 mesh 10%, spherical graphite 500 mesh 80%, spherical graphite 800 mesh 10%. The above-mentioned spherical graphite powder was mixed evenly and then put into an oven and dried at 120° C. for 12 hours. Weighing by weight: 60% of the dried spherical graphite powder, 1% of quartz glass fiber, 1% of mullite fiber, and 38% of ceramic core plasticizer. Raise the temperature of the mixer to 100°C, add ceramic core plasticizer, and after it is completely melted, add the dried graphite into the mixer in proportion, stir for 4 hours, and take it out to obtain the graphite core slurry.
[0041] b. Forming
[0042] Put the prepared graphite core slurry into a ceramic core injection molding machine to prepare a graphite core green body.
[0043] c. Graphite core firing
[0044] The graphite core green body was embedded in 200-mesh alumina powder and fired at a firi...
PUM
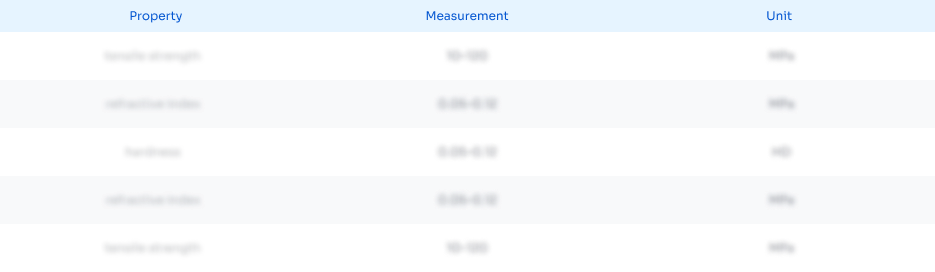
Abstract
Description
Claims
Application Information

- R&D Engineer
- R&D Manager
- IP Professional
- Industry Leading Data Capabilities
- Powerful AI technology
- Patent DNA Extraction
Browse by: Latest US Patents, China's latest patents, Technical Efficacy Thesaurus, Application Domain, Technology Topic, Popular Technical Reports.
© 2024 PatSnap. All rights reserved.Legal|Privacy policy|Modern Slavery Act Transparency Statement|Sitemap|About US| Contact US: help@patsnap.com