Propane dehydrogenation catalyst and preparation method thereof
A propane dehydrogenation and catalyst technology, which is applied in catalyst activation/preparation, catalyst, catalyst carrier and other directions, can solve the problems of catalyst deactivation, instability of platinum metal and tin, poor stability, etc., and achieves good application prospects and improved conversion rate. , the effect of selective enhancement
- Summary
- Abstract
- Description
- Claims
- Application Information
AI Technical Summary
Problems solved by technology
Method used
Image
Examples
Embodiment 1
[0032] 1.1. Preparation of carrier
[0033] Weigh 6.41g of magnesium nitrate, add 50mL of absolute ethanol, and sonicate for 0.5h; at the same time, weigh 10.21g of aluminum isopropoxide, pour it into 100mL of absolute ethanol, sonicate for 0.5h, and stir magnetically until the aluminum isopropoxide ethanol solution forms an emulsified cloud solution, slowly add the magnesium nitrate ethanol solution dropwise to the aluminum isopropoxide alcohol solution, the dropping rate is 2s / 1 drop; then continue magnetic stirring for 2h, and then transfer the resulting mixed solution to a hydrothermal kettle for alcohol thermal reaction, the reaction The temperature is 135°C, and the reaction time is 8h. Then add 0.25 g of ammonium borate and continue aging for 12 hours. The reaction product was volatilized at room temperature, then dried at 110°C for 8 hours, the solid product was ground, the solid powder was sieved, the sample was collected, and the crystal plane-oriented magnesium-alu...
Embodiment 2
[0042] 2.1, carrier preparation
[0043]Weigh 6.41g of magnesium nitrate, add 50mL of absolute ethanol, and ultrasonicate for 0.5h; at the same time, weigh 10.21g of aluminum isopropoxide, add 100mL of absolute ethanol, ultrasonicate for 0.5h, and stir magnetically until the aluminum isopropoxide ethanol solution forms an emulsion , slowly add the magnesium nitrate ethanol solution dropwise to the aluminum isopropoxide ethanol solution, the dropping rate is 5s / 1 drop, and then continue magnetic stirring for 2h, then transfer the resulting mixed solution to a hydrothermal kettle for alcohol thermal reaction, the reaction temperature 135°C, reaction time 8h. Then add 12.5 g of ammonium borate and continue to age for 12 hours. The reaction product was volatilized at room temperature, then dried at 110°C for 8 hours, the solid product was ground, the solid powder was sieved, the sample was collected, and it was calcined at 800°C for 9 hours to obtain a crystal plane-oriented magn...
Embodiment 3
[0051] 3.1. Vector preparation
[0052] Weigh 6.41g of magnesium nitrate, add 50mL of absolute ethanol, and ultrasonicate for 0.5h; at the same time, weigh 10.21g of aluminum isopropoxide, add 100mL of absolute ethanol, ultrasonicate for 0.5h, and stir magnetically until the aluminum isopropoxide ethanol solution forms an emulsion , slowly add magnesium nitrate ethanol solution dropwise to the emulsion of aluminum isopropoxide ethanol solution, the dropping rate is 2s / 1 drop, continue magnetic stirring for 2h, and then transfer the resulting mixed solution to a hydrothermal kettle for alcohol thermal reaction , the reaction temperature is 120°C, and the reaction time is 12h. Then add 2.5g of ammonium borate and continue aging for 12h. The reaction product was evaporated at room temperature for 12 hours, then dried at 110°C for 8 hours, ground to obtain a solid sample powder, sieved, and calcined at 600°C for 12 hours to obtain a crystal plane-oriented magnesium-aluminum spine...
PUM
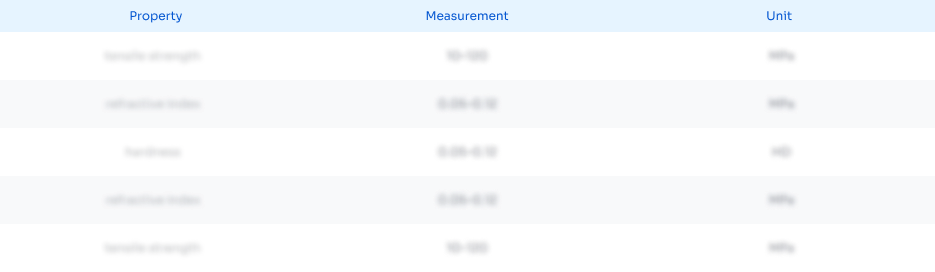
Abstract
Description
Claims
Application Information

- Generate Ideas
- Intellectual Property
- Life Sciences
- Materials
- Tech Scout
- Unparalleled Data Quality
- Higher Quality Content
- 60% Fewer Hallucinations
Browse by: Latest US Patents, China's latest patents, Technical Efficacy Thesaurus, Application Domain, Technology Topic, Popular Technical Reports.
© 2025 PatSnap. All rights reserved.Legal|Privacy policy|Modern Slavery Act Transparency Statement|Sitemap|About US| Contact US: help@patsnap.com