High carbon brake disc proportion and production process thereof
A production process and brake disc technology, applied in the field of high-carbon brake disc ratio and its production process, can solve the problems of shrinkage, poor performance, easy to cause cracks, etc., to prevent clumping and excellent tensile strength and hardness, to avoid the effect of bred recession
- Summary
- Abstract
- Description
- Claims
- Application Information
AI Technical Summary
Problems solved by technology
Method used
Image
Examples
Embodiment 1
[0035] Proportion of high-carbon brake disc, the proportion of each component in every 100g of high-carbon brake disc is as follows (unit: g):
[0036] C: 3.66;
[0037] Si: 1.8;
[0038] Mn: 0.72;
[0039] P: 0.043;
[0040] S: 0.087;
[0041] Cr: 0.26;
[0042] Sn: 0.063;
[0043] Cu: 0.32;
[0044] Nb: 0.081.
Embodiment 2
[0046] Proportion of high-carbon brake disc, the proportion of each component in every 100g of high-carbon brake disc is as follows (unit: g):
[0047] C:3.:7;
[0048] Si: 1.76;
[0049] Mn: 0.75;
[0050] P: 0.45;
[0051] S: 0..091;
[0052] Cr: 0.27;
[0053] Sn: 0.064;
[0054] Cu: 0.32;
[0055] Nb: 0.078.
Embodiment 3
[0057] Proportion of high-carbon brake disc, the proportion of each component in every 100g of high-carbon brake disc is as follows (unit: g):
[0058] C: 3.70;
[0059] Si: 1.78;
[0060] Mn: 0.77;
[0061] P: 0.042;
[0062] S: 0.085;
[0063] Cr: 0.26;
[0064] Sn: 0.072;
[0065] Cu: 0.33;
[0066] Nb: 0.08.
PUM
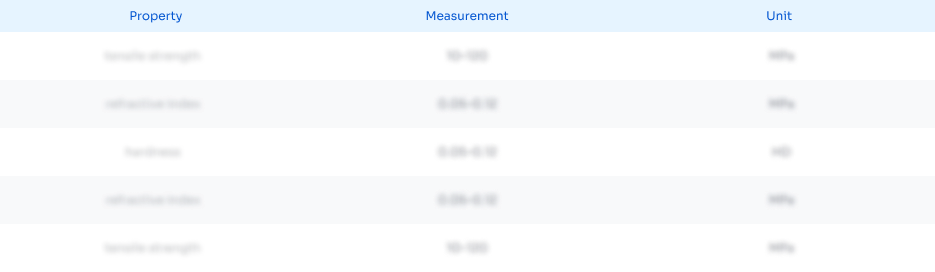
Abstract
Description
Claims
Application Information

- R&D
- Intellectual Property
- Life Sciences
- Materials
- Tech Scout
- Unparalleled Data Quality
- Higher Quality Content
- 60% Fewer Hallucinations
Browse by: Latest US Patents, China's latest patents, Technical Efficacy Thesaurus, Application Domain, Technology Topic, Popular Technical Reports.
© 2025 PatSnap. All rights reserved.Legal|Privacy policy|Modern Slavery Act Transparency Statement|Sitemap|About US| Contact US: help@patsnap.com