A kind of fluorination process containing 1,3-dioxolane ester or 1,3-dioxane ester perfluorinated compound
A technology for dioxane and dioxolane, which is applied in the field of perfluorinated compound synthesis, can solve the problems of low purity and yield, difficult process control and the like, and achieves simple method, low cost and high yield Effect
- Summary
- Abstract
- Description
- Claims
- Application Information
AI Technical Summary
Problems solved by technology
Method used
Image
Examples
Embodiment 1
[0067] Dissolve 150 grams of 2,4,5-trimethyl-1,3-dioxolane-2-acid methyl ester and 6 grams of perfluorooctanesulfonic acid in 300 milliliters of FC-75, and fully stir to form a raw material solution. Add 2.5 liters of FC-75 and 15 grams of cobalt trifluoride into a 5-liter nickel reactor, stir well and keep it at minus 10 degrees, and the temperature of the condenser is minus 20 degrees. Pass nitrogen gas for one hour to drive away the air in the reaction system, then pass 20% fluorine gas (diluted with nitrogen) at a rate of 0.5L / min for half an hour, then slowly increase the flow rate of fluorine gas to 0.8L / min, and within 30 hours Inject the raw material solution. The temperature of the reaction system was maintained at minus 10 degrees. After the injection of the raw material solution, keep the flow rate of the fluorine gas constant, and continue to pass the fluorine gas for half an hour. After the reaction was finished, the product was discharged from the discharge val...
Embodiment 2
[0069] Dissolve 200 grams of 2-methyl-1,3-dioxolane-2-acid methyl ester and 8 grams of perfluorononanoic acid in 300 milliliters of FC-75, and fully stir to form a raw material solution. Add 2.5 liters of FC-75 and 20 grams of cobalt trifluoride into a 5-liter nickel reactor, stir well and keep it at minus 15 degrees, and the temperature of the condenser is minus 30 degrees. Pass nitrogen for one hour to drive away the air in the reaction system, then pass in 20% fluorine gas (diluted with nitrogen) for half an hour at a rate of 0.5L / min, then slowly increase the flow rate of fluorine gas to 1L / min, and inject it within 30 hours raw material liquid. The temperature of the reaction system was maintained at minus 15 degrees. After the injection of the raw material solution, keep the flow rate of the fluorine gas constant, and continue to pass the fluorine gas for half an hour. After the reaction, the product was discharged from the discharge valve, and after the crude product ...
Embodiment 3
[0071] Dissolve 120 grams of 2,4,6-trimethyl-1,3-dioxane-2-oic acid methyl ester and 15 grams of perfluorooctane sulfonic acid in 300 ml of FC-75, stir well to form raw materials liquid. Add 2.5 liters of FC-75 and 15 grams of cobalt trifluoride into a 5-liter nickel reactor, stir well and keep it at zero degrees, and the temperature of the condenser is minus 20 degrees. Pass nitrogen for one hour to drive away the air in the reaction system, then pass in 20% fluorine gas (diluted with nitrogen) for half an hour at a rate of 0.5L / min, then slowly increase the flow rate of fluorine gas to 1L / min, and inject it within 30 hours raw material liquid. The temperature of the reaction system was maintained at zero degrees. After the injection of the raw material solution, keep the flow rate of the fluorine gas constant, and continue to pass the fluorine gas for half an hour. After the reaction, the product is discharged from the discharge valve, and the crude product is obtained by...
PUM
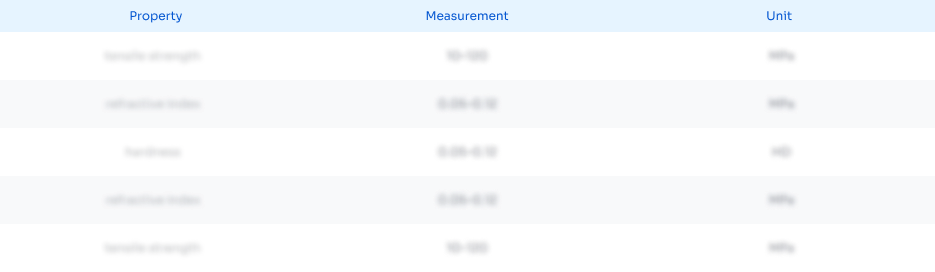
Abstract
Description
Claims
Application Information

- R&D
- Intellectual Property
- Life Sciences
- Materials
- Tech Scout
- Unparalleled Data Quality
- Higher Quality Content
- 60% Fewer Hallucinations
Browse by: Latest US Patents, China's latest patents, Technical Efficacy Thesaurus, Application Domain, Technology Topic, Popular Technical Reports.
© 2025 PatSnap. All rights reserved.Legal|Privacy policy|Modern Slavery Act Transparency Statement|Sitemap|About US| Contact US: help@patsnap.com