Environment-friendly method for preparing silicon nitride ceramic green body by gel injection molding
A technology of gel injection molding and silicon nitride ceramics, which is applied in the field of ceramic material molding and preparation, can solve the problems of green body deformation, low strength, and easy damage of the green body, and achieve high molding precision and good uniformity Effect
- Summary
- Abstract
- Description
- Claims
- Application Information
AI Technical Summary
Problems solved by technology
Method used
Examples
Embodiment 1
[0023] (1) Silicon nitride powder pretreatment: In the ball mill, add silicon nitride: 960g, scandium trioxide: 10g, soybean oil: 30g, turn on the ball mill and grind for 2 hours, dry to get the pretreated silicon nitride powder , the particle size is between 0.15~0.25μm;
[0024] (2) Gel solution preparation: In the reactor, add deionized water: 950 mL, Carbomer 941: 10g, ammonium citrate: 30g, ethylenediamine: 10g, stir and dissolve to obtain a gel solution;
[0025] (3) Preparation of silicon nitride ceramic slurry: In a ball mill, add separately, pre-treated silicon nitride powder: 500 mL, gel solution: 450 mL, ammonium oxalate: 50 g, grind for 11 hours, vacuum defoaming treatment, get Silicon nitride ceramic slurry;
[0026] (4) Preparation of silicon nitride green body: Inject the silicon nitride ceramic slurry in step (3) into the mold, heat slowly, and keep the temperature at 85±3°C for 17 hours. After natural cooling, dry and demould to obtain nitrogen Silicon biscu...
Embodiment 2
[0028] (1) Silicon nitride powder pretreatment: In the ball mill, add silicon nitride: 950g, lanthanum oxide: 20g, peanut oil: 30g, turn on the ball mill and grind for 2 hours, dry to get the pretreated silicon nitride powder, its The particle size is between 0.15~0.25μm;
[0029] (2) Gel solution preparation: In the reactor, add deionized water: 980 mL, Carbomer 941: 5g, ammonium citrate: 10g, ethylenediamine: 5g, stir and dissolve to obtain a gel solution;
[0030] (3) Preparation of silicon nitride ceramic slurry: In a ball mill, add separately, pre-treat silicon nitride powder: 480 mL, gel solution: 460 mL, ammonium oxalate: 60 g, grind for 10 hours, vacuum defoaming treatment, get Silicon nitride ceramic slurry;
[0031] (4) Preparation of silicon nitride biscuit: inject the silicon nitride ceramic slurry in step (3) into the mold, heat slowly, and keep the temperature at 85±3°C for 16 hours. After natural cooling, dry and demould to obtain nitrided Silicon blank.
Embodiment 3
[0033] (1) Silicon nitride powder pretreatment: In the ball mill, add silicon nitride: 970g, zirconium dioxide: 2g, rapeseed oil: 28g, turn on the ball mill and grind for 2 hours, dry to obtain pretreated silicon nitride powder body, its particle size is between 0.15 and 0.25 μm;
[0034] (2) Gel solution preparation: In the reactor, add deionized water: 940 mL, Carbomer 941: 20g, ammonium citrate: 20g, ethylenediamine: 20g, stir and dissolve to obtain a gel solution;
[0035] (3) Preparation of silicon nitride ceramic slurry: In a ball mill, add separately, pretreat silicon nitride powder: 530 mL, gel solution: 440 mL, ammonium oxalate: 30 g, grind for 12 hours, vacuum defoaming treatment, get Silicon nitride ceramic slurry;
[0036] (4) Preparation of silicon nitride biscuit: inject the silicon nitride ceramic slurry in step (3) into the mold, heat slowly, and keep the temperature at 85±3°C for 18 h. After natural cooling, dry and demould to obtain nitrogen Silicon biscuit...
PUM
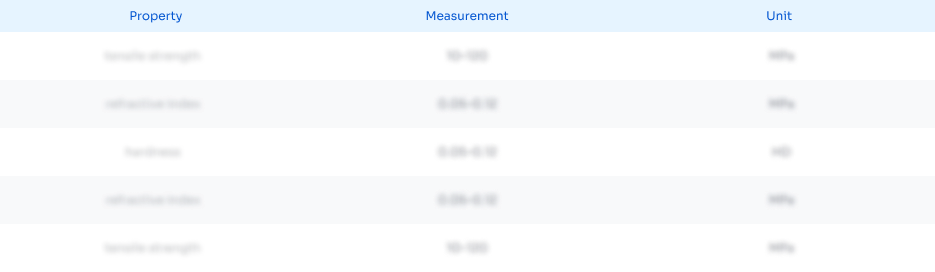
Abstract
Description
Claims
Application Information

- R&D
- Intellectual Property
- Life Sciences
- Materials
- Tech Scout
- Unparalleled Data Quality
- Higher Quality Content
- 60% Fewer Hallucinations
Browse by: Latest US Patents, China's latest patents, Technical Efficacy Thesaurus, Application Domain, Technology Topic, Popular Technical Reports.
© 2025 PatSnap. All rights reserved.Legal|Privacy policy|Modern Slavery Act Transparency Statement|Sitemap|About US| Contact US: help@patsnap.com