Production method of PCB (printed circuit board) and PCB
A production method and graphic technology, which is applied in the direction of multilayer circuit manufacturing, printed circuit manufacturing, conductive pattern layout details, etc., can solve the problems affecting the performance and assembly of the circuit graphic layer, uneven surface, layered blistering, etc., to achieve maintenance Surface flatness and solderability, smooth coating, and enhanced bonding effect
- Summary
- Abstract
- Description
- Claims
- Application Information
AI Technical Summary
Problems solved by technology
Method used
Image
Examples
Embodiment 2
[0075] see figure 2 , the embodiment of the present invention also provides a PCB for an AC charging pile, the PCB includes an upper PCB sub-board 11 , a prepreg 13 , an inner core board 10 , a prepreg 13 and a lower PCB sub-board 12 that are sequentially stacked and pressed together. , the inner layer core board 10 is made with an inner layer circuit pattern by the first electroplating, and the outer layer circuit pattern is made on the upper layer PCB sub-board 11 and the lower layer PCB sub-board 12 through the second electroplating;
[0076] The outer layer circuit pattern is also provided with at least two copper-drawing holes that run through the PCB and avoid the inner-layer circuit pattern; one end of the copper-drawing hole is connected to the surface copper of the outer layer circuit pattern, so The other end of the drawn copper hole copper avoids the outer circuit pattern on the other side;
[0077] The pattern area of the outer circuit pattern is covered with a...
PUM
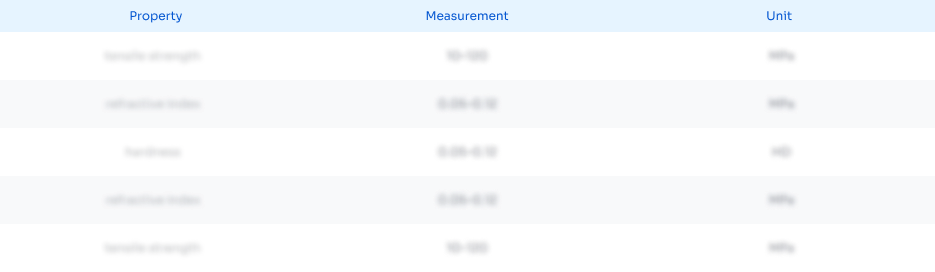
Abstract
Description
Claims
Application Information

- Generate Ideas
- Intellectual Property
- Life Sciences
- Materials
- Tech Scout
- Unparalleled Data Quality
- Higher Quality Content
- 60% Fewer Hallucinations
Browse by: Latest US Patents, China's latest patents, Technical Efficacy Thesaurus, Application Domain, Technology Topic, Popular Technical Reports.
© 2025 PatSnap. All rights reserved.Legal|Privacy policy|Modern Slavery Act Transparency Statement|Sitemap|About US| Contact US: help@patsnap.com