AGM partition production system
A production system and separator technology, applied in electrical components, circuits, battery pack components, etc., can solve the problems of wasting heat energy, prolonging drying time, reducing production efficiency and safety, and reducing production costs and speeding up molding. Speed, the effect of improving molding quality
- Summary
- Abstract
- Description
- Claims
- Application Information
AI Technical Summary
Problems solved by technology
Method used
Image
Examples
Embodiment 1
[0028] Such as figure 1 As shown, an AGM separator production system includes a molding device and a drying device. The molding device includes a uniform material conveying device and a water absorption device. Feed port 1, the other side of the uniform material tank is provided with a discharge port 11, and multiple stirring and flow control devices are arranged in the uniform material tank. The raw material slurry of the AGM separator enters the uniform material tank through the feed port and is stirred The flow control device flows to the discharge port, and then flows out from the discharge port. The stirring flow control device includes a material partition plate 6 arranged on the bottom surface of the inner wall of the uniform material tank, a flow control plate 10 arranged on the top of the internal wall of the uniform material tank, and a flow control plate arranged on the partition wall. The stirring device between the material plate and the flow control plate, the st...
PUM
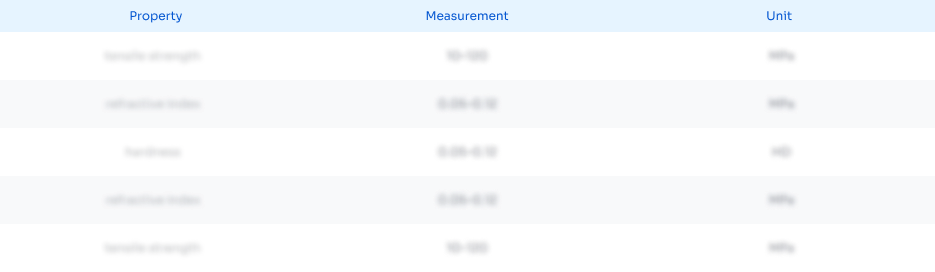
Abstract
Description
Claims
Application Information

- R&D
- Intellectual Property
- Life Sciences
- Materials
- Tech Scout
- Unparalleled Data Quality
- Higher Quality Content
- 60% Fewer Hallucinations
Browse by: Latest US Patents, China's latest patents, Technical Efficacy Thesaurus, Application Domain, Technology Topic, Popular Technical Reports.
© 2025 PatSnap. All rights reserved.Legal|Privacy policy|Modern Slavery Act Transparency Statement|Sitemap|About US| Contact US: help@patsnap.com