Hydraulic driving automatic exchange workbench of closed mechanical press
A mechanical press and automatic exchange technology, applied in the direction of forging/pressing/hammering machinery, forging presses, forging presses, etc., can solve the problems of inability to accurately locate the clamping mechanism, cumulative errors, and damage to the accuracy of machine tools
- Summary
- Abstract
- Description
- Claims
- Application Information
AI Technical Summary
Problems solved by technology
Method used
Image
Examples
Embodiment Construction
[0047] In order to clearly illustrate the technical features of this solution, the present invention will be described in detail below through specific implementation modes and in conjunction with the accompanying drawings.
[0048] Such as Figure 7-12 As shown, a hydraulically driven automatic exchange workbench of a closed mechanical press includes a base 1, on which a rail 2 is arranged, and on the rail 2, one or two exchange workbench bodies 3 are arranged, and the exchange workbench body 3 The four corners are respectively equipped with roller jacking devices 4, the exchange table body 3 is set on the rail 2 through the roller jacking device 4, and a set of multi-stage hydraulic cylinders are installed between each exchange table body 3 and the base 1 Device 5, multi-stage hydraulic cylinder drive device 5 includes a multi-stage hydraulic cylinder 501 arranged at one end of the base 1, the end of the piston rod of the multi-stage hydraulic cylinder 501 is vertically prov...
PUM
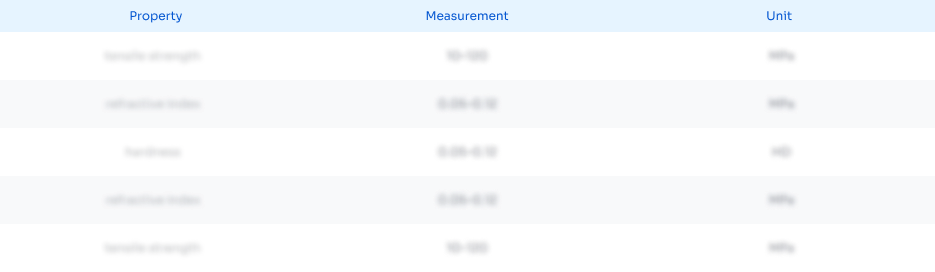
Abstract
Description
Claims
Application Information

- R&D Engineer
- R&D Manager
- IP Professional
- Industry Leading Data Capabilities
- Powerful AI technology
- Patent DNA Extraction
Browse by: Latest US Patents, China's latest patents, Technical Efficacy Thesaurus, Application Domain, Technology Topic, Popular Technical Reports.
© 2024 PatSnap. All rights reserved.Legal|Privacy policy|Modern Slavery Act Transparency Statement|Sitemap|About US| Contact US: help@patsnap.com