Method for synthesizing light calcium-silicate thermal insulation material
An insulation material, calcium silicate technology, applied in the field of calcium silicate insulation materials, can solve the problems of poor crystallization degree of xonotlite crystal, incomplete crystallization reaction of raw materials, uneven fiber dispersion, etc., and achieve liquid-solid ratio Low temperature, excellent product performance and heat preservation effect, and complete crystallization reaction
- Summary
- Abstract
- Description
- Claims
- Application Information
AI Technical Summary
Problems solved by technology
Method used
Image
Examples
Embodiment 1
[0040] This embodiment provides a method for synthesizing a lightweight calcium silicate thermal insulation material under high temperature and high pressure dynamic hydrothermal synthesis using fly ash desilication lye, reinforcing fiber, and milk of lime. The method includes the following steps:
[0041] (1) Preparation of refined sodium silicate solution: take 20g of high-purity quartz sand, use a pulverizer to finely grind the particle size below 0.1mm, then add it to 81.43g of sodium hydroxide solution with a concentration of 14%, and form after stirring Slurry, under this condition, the mass ratio of sodium hydroxide and quartz sand dry basis is controlled to be 4:3, the temperature of the slurry is raised to 195 ° C, 1.9Mpa, and the reaction is carried out for 2.5 hours under this condition. After the reaction, the slurry is solid-liquid Separate, and finely filter the crude sodium silicate solution through a leaf filter, and return the solid waste to the quartz sand fee...
Embodiment 2
[0047] This embodiment provides a method for synthesizing a lightweight calcium silicate thermal insulation material under high temperature and high pressure dynamic hydrothermal synthesis using fly ash desilication lye, reinforcing fiber, and milk of lime. The method includes the following steps:
[0048] (1) Preparation of refined sodium silicate solution: take 20g of high-purity quartz sand, and use a pulverizer to finely grind the particle size below 0.1mm, then add it to 75g of sodium hydroxide solution with a concentration of 16%, and form after stirring Slurry, under this condition, the mass ratio of sodium hydroxide and quartz sand dry basis is controlled to be 3:2, the temperature of the slurry is raised to 205 ° C, 2.1Mpa, and the reaction is carried out for 3.5 hours under this condition. After the reaction, the slurry is solid-liquid Separate, and finely filter the crude sodium silicate solution through a leaf filter, and return the solid waste to the quartz sand fe...
Embodiment 3
[0054] This embodiment provides a method for synthesizing a lightweight calcium silicate thermal insulation material under high temperature and high pressure dynamic hydrothermal synthesis using fly ash desilication lye, reinforcing fiber, and milk of lime. The method includes the following steps:
[0055] (1) Preparation of refined sodium silicate solution: take 20g of high-purity quartz sand, and use a pulverizer to grind it finely, then add it into 64g of sodium hydroxide solution with a concentration of 30%, form a slurry after stirring, and control under this condition The mass ratio of sodium hydroxide and quartz sand dry basis is 2:1, the temperature of the slurry is raised to 225°C and 2.5Mpa, and the reaction is carried out for 11 hours under these conditions. After the reaction, the slurry is separated from the solid and liquid, and the sodium silicate is The liquid is finely filtered through the leaf filter, and the solid waste is returned to the quartz sand feed por...
PUM
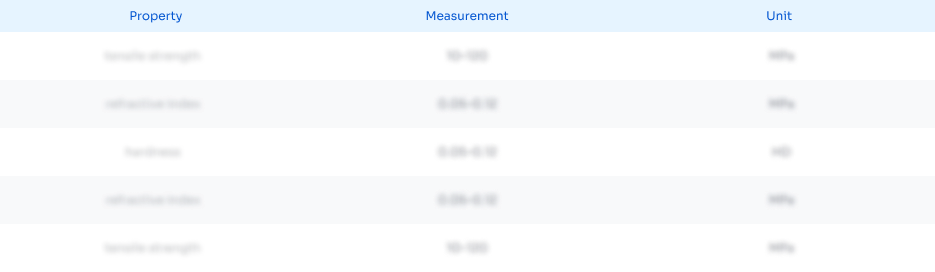
Abstract
Description
Claims
Application Information

- R&D
- Intellectual Property
- Life Sciences
- Materials
- Tech Scout
- Unparalleled Data Quality
- Higher Quality Content
- 60% Fewer Hallucinations
Browse by: Latest US Patents, China's latest patents, Technical Efficacy Thesaurus, Application Domain, Technology Topic, Popular Technical Reports.
© 2025 PatSnap. All rights reserved.Legal|Privacy policy|Modern Slavery Act Transparency Statement|Sitemap|About US| Contact US: help@patsnap.com