Laser 3D printing platform for manufacturing cast sand mold
A 3D printing and production platform technology, applied in the direction of casting molding equipment, casting molds, casting mold components, etc., can solve the problems of affecting equipment progress, increasing equipment costs, prolonging the production cycle of parts, etc., to achieve dust pollution reduction, stable structure, The effect of improving efficiency
- Summary
- Abstract
- Description
- Claims
- Application Information
AI Technical Summary
Problems solved by technology
Method used
Image
Examples
Embodiment Construction
[0015] The specific implementation manner of the present invention will be further described below in conjunction with the accompanying drawings.
[0016] Such as figure 1 , 2 As shown, the laser 3D printing platform for making casting sand molds of the present invention includes a vacuum feeding pipe 1, a vacuum pump 2, a sand material conveying pipe 3, a coaxial powder feeding device 4, a box body 5, an X-axis guide rail 6, and a Y-axis guide rail 7. Motion guide rail support 8, sand mold making platform 9, sand mold shifting car 10, sand mold shifting car guide rail 11, lifting platform 12, guiding optical axis 13, screw elevator 14, servo motor 15, base 16. The vacuum feeding pipe 1 is connected to the sand material box, and the sand material is transported to the laser 3D printer through the vacuum pump 2. The sand material delivery pipe 3 transports the sand material to the coaxial powder feeding device 4. The X-axis guide rail 6 and the Y-axis The guide rail 7 drives ...
PUM
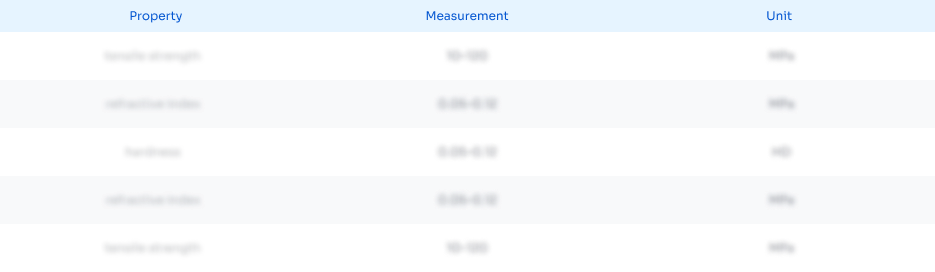
Abstract
Description
Claims
Application Information

- R&D
- Intellectual Property
- Life Sciences
- Materials
- Tech Scout
- Unparalleled Data Quality
- Higher Quality Content
- 60% Fewer Hallucinations
Browse by: Latest US Patents, China's latest patents, Technical Efficacy Thesaurus, Application Domain, Technology Topic, Popular Technical Reports.
© 2025 PatSnap. All rights reserved.Legal|Privacy policy|Modern Slavery Act Transparency Statement|Sitemap|About US| Contact US: help@patsnap.com