Curve fitting method for ensuring global G2 continuity of tool path
A curve fitting and tool path technology, applied in the direction of digital control, electrical program control, etc., can solve problems such as application limitations, accelerated tool wear, part contour machining accuracy and poor surface quality.
- Summary
- Abstract
- Description
- Claims
- Application Information
AI Technical Summary
Problems solved by technology
Method used
Image
Examples
specific Embodiment
[0079] The present invention provides a curve fitting method that ensures the overall G2 continuity of the tool track, comprising the following steps:
[0080] (1) Establish a B-spline curve;
[0081] According to the discrete tool trajectory, first identify the feature points, then divide the discrete data points between every two adjacent feature points into several small intervals, and finally establish the B-spline curve in sections. The present invention does not make too many descriptions on the B-spline segment fitting. For details, please refer to He S, et al. A chord error conforming tool path B-spline fitting method for NC machining based on energy minimization and LSPIA. Journal of Computational Design and Engineering (2015).
[0082] (2) Screen splines to determine the splines that need to be bridged
[0083] Not all splines are suitable for G2 bridging. Because the feature point is a point that cannot be changed, the spline curve segmented by the feature point ...
PUM
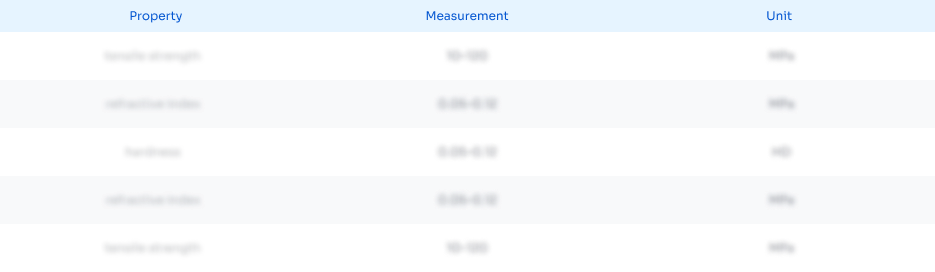
Abstract
Description
Claims
Application Information

- R&D
- Intellectual Property
- Life Sciences
- Materials
- Tech Scout
- Unparalleled Data Quality
- Higher Quality Content
- 60% Fewer Hallucinations
Browse by: Latest US Patents, China's latest patents, Technical Efficacy Thesaurus, Application Domain, Technology Topic, Popular Technical Reports.
© 2025 PatSnap. All rights reserved.Legal|Privacy policy|Modern Slavery Act Transparency Statement|Sitemap|About US| Contact US: help@patsnap.com