Rare earth-aluminum-titanium-boron alloy and preparation method thereof
A rare earth aluminum, titanium boron technology, applied in the application field of aluminum alloy, can solve the problems of loss of refining ability, easy aggregation of particles, poisoning reaction, etc. Effect
- Summary
- Abstract
- Description
- Claims
- Application Information
AI Technical Summary
Problems solved by technology
Method used
Examples
preparation example Construction
[0023] The preparation method of rare earth aluminum titanium boron alloy specifically comprises the following steps:
[0024] Step 1: Weighing raw materials, raw materials include: titanium powder or aluminum-titanium master alloy, boron powder or aluminum-boron master alloy, rare earth metal or rare earth aluminum master alloy, aluminum ingot, non-rare earth raw materials;
[0025] Non-rare earth raw materials include: metal strontium, aluminum-strontium master alloy, metal copper, aluminum-copper master alloy, metal iron, aluminum-iron master alloy, magnesium ingot, aluminum-magnesium master alloy, silicon, aluminum-silicon master alloy, metal zinc, aluminum-zinc master alloy alloy. It is also possible not to add non-rare earth raw materials.
[0026] Step 2: After heating up and melting the aluminum ingot, adding raw materials for reaction;
[0027] After heating and melting, the melt temperature is controlled at 1000-1500°C.
[0028] Induction furnace, resistance furna...
Embodiment 1
[0037] (1) Weigh titanium powder, boron powder, metal lanthanum, industrial pure aluminum as required;
[0038] (2) After heating and melting industrial pure aluminum in the induction furnace, various raw materials are added for reaction, and the temperature of the melt is controlled at 1500°C after heating and melting;
[0039] (3) Refining after stirring until the melt reaction is complete, the stirring time is 10min, nitrogen gas is used for refining, and the refining time is 5min;
[0040] (4) Remove slag after heat preservation, cast into rods to obtain rare earth aluminum titanium boron alloy; extrude into wires after forming rods, the heat preservation temperature is 1500 ℃, and the heat preservation time is 60 minutes.
[0041] The composition of the rare-earth aluminum-titanium-boron alloy is (by weight percentage): 3.0% titanium, 3.0% boron, 3.0% La, and the balance is aluminum.
Embodiment 2
[0043] (1) Weigh titanium powder, aluminum-boron master alloy, metal cerium, metal neodymium, and industrial pure aluminum as required;
[0044] (2) After heating up and melting industrial pure aluminum in the resistance furnace, various raw materials are added for reaction, and the temperature of the melt is controlled at 1400°C after heating up and melting;
[0045] (3) Refining after stirring until the melt reaction is complete, the stirring time is 30min, the refining adopts argon, and the refining time is 15min;
[0046] (4) Remove slag after heat preservation, and cast into an ingot to obtain a rare earth aluminum titanium boron alloy. The heat preservation temperature is 1400° C. and the heat preservation time is 50 minutes.
[0047] The composition of the rare-earth aluminum-titanium-boron alloy is (by weight percentage): 4.0% titanium, 2.5% boron, 1.0% cerium, 1.0% neodymium, and the balance is aluminum.
PUM
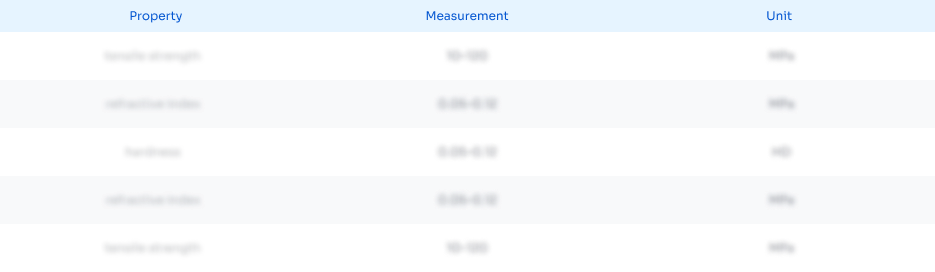
Abstract
Description
Claims
Application Information

- R&D
- Intellectual Property
- Life Sciences
- Materials
- Tech Scout
- Unparalleled Data Quality
- Higher Quality Content
- 60% Fewer Hallucinations
Browse by: Latest US Patents, China's latest patents, Technical Efficacy Thesaurus, Application Domain, Technology Topic, Popular Technical Reports.
© 2025 PatSnap. All rights reserved.Legal|Privacy policy|Modern Slavery Act Transparency Statement|Sitemap|About US| Contact US: help@patsnap.com