A process for producing natural gas from synthetic gas
A synthesis gas and natural gas technology, which is applied in the direction of gas fuel, petroleum industry, fuel, etc., can solve the problems of high energy consumption and large circulating gas volume of the circulating gas compressor, so as to reduce the total energy consumption, reduce the circulating gas volume, and control the reaction temperature rise Effect
- Summary
- Abstract
- Description
- Claims
- Application Information
AI Technical Summary
Problems solved by technology
Method used
Image
Examples
Embodiment 1
[0036] When the four-stage methanation reaction is adopted, that is, N=4, M=1, a process for producing natural gas from synthesis gas, the process flow is as follows figure 2 shown, including the following steps:
[0037] Feed amount of raw material synthesis gas 1 is 449kNm 3 / h, temperature 40°C, pressure 3.4MPaG, volume percent composition: H 2 : 46.22, CO: 14.28, CO 2 : 38.40, CH 4 : 0.00, N 2 : 0.23, H 2 S: 0.87.
[0038] The raw material synthesis gas 1 is desulfurized by a desulfurization unit 12 to remove H 2 S and other sulfur-containing components to obtain desulfurized gas 19 with a total sulfur content of <0.1ppm, and the removed sulfur-containing gas 24 is sent outside the boundary area;
[0039] The obtained desulfurized gas 19 enters the preheater 15 for preheating, and the preheated gas is divided into two streams, the first stream of desulfurized gas 20 and the recycle gas from the outlet of the recycle gas compressor 11 and the recycle gas from the de...
Embodiment 2
[0057] When the four-stage methanation reaction is adopted, that is, N=4, M=2, a process for producing natural gas from synthesis gas, the process flow is as follows Figure 4 shown, including the following steps:
[0058] Feed amount of raw material synthesis gas 1 315kNm 3 / h, temperature 40°C, pressure 3.65MPaG, volume percent composition: H 2 : 40.31, CO: 12.06, CO 2 : 33.92, CH 4 : 12.69, N 2 : 0.23, H 2 S: 0.78.
[0059] The raw material synthesis gas 1 is desulfurized by a desulfurization unit 12 to remove H 2 S and other sulfur-containing components to obtain desulfurized gas 19 with a total sulfur content of <0.1ppm, and the removed sulfur-containing gas 24 is sent outside the boundary area.
[0060] The resulting sweetened gas 19 is the same as that from deCO 2 After the methane desorption gas 14 of the device 13 is mixed, it enters the preheater 15 for preheating. The preheated gas is divided into two streams. The temperature of the gas reaches 320°C, and e...
Embodiment 3
[0078] Adopt the same processing device and feed gas as embodiment 1, its flow process is as follows figure 2 As shown, the difference is:
[0079] (1) The flow ratio of the first stream of desulfurized gas 20 and desulfurized gas 19 is 0.2;
[0080] (2) The ratio of the second product gas 23a flow to the sum of the first product gas 22a and the second product gas 23a flow is 0.1;
[0081] (3) The material inlet temperature of the first methanation reactor is 250°C, the material inlet temperature of the second methanation reactor is 190°C, the material inlet temperature of the third methanation reactor is 200°C, and the fourth methanation reactor The material inlet temperature of the device was 190°C.
[0082] After testing, the circulating gas volume of the circulating gas compressor 11 is about 10.6kNm 3 / h, the required compression work is about 52kW.
PUM
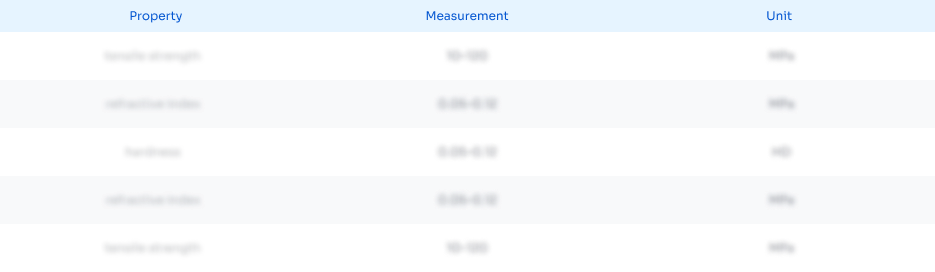
Abstract
Description
Claims
Application Information

- R&D Engineer
- R&D Manager
- IP Professional
- Industry Leading Data Capabilities
- Powerful AI technology
- Patent DNA Extraction
Browse by: Latest US Patents, China's latest patents, Technical Efficacy Thesaurus, Application Domain, Technology Topic, Popular Technical Reports.
© 2024 PatSnap. All rights reserved.Legal|Privacy policy|Modern Slavery Act Transparency Statement|Sitemap|About US| Contact US: help@patsnap.com