Nano-structure graphite carbon material as well as preparation method and application thereof
A nanostructure, graphitic carbon technology, applied in the direction of nanocarbon, structural parts, chemical instruments and methods, etc., can solve the problems of poor conductivity, reduced specific surface area, large proportion of large pores, etc., to speed up charging and discharging , Appropriate specific surface area, and the effect of increasing capacity
- Summary
- Abstract
- Description
- Claims
- Application Information
AI Technical Summary
Problems solved by technology
Method used
Image
Examples
preparation example Construction
[0025] see figure 1 , figure 1 It is a flowchart of a preferred embodiment of a method for preparing a nanostructured graphite carbon material of the present invention, as shown in the figure, including steps:
[0026] S10. After mixing and soaking the plant material and filler for a predetermined time according to a predetermined mass ratio, rolling and extruding are performed to obtain a rolled material;
[0027] S20. Under an inert atmosphere, heating the rolled material to 180-2100° C. and keeping it warm for 0.5-24 hours to obtain a carbonized material;
[0028] S30. Under centrifugation or vacuum conditions, immerse the carbonized material in a strong alkali solution, then heat the carbonized material to 400-1200° C. under an inert atmosphere, and keep it warm for 0.5-24 hours to obtain an activated material;
[0029] S40. Centrifugally clean the activated material, then soak it in a solution containing metal ions, dry it and heat it to 400-1200° C. under an inert atmo...
Embodiment 1
[0047] 1. Rolling: After cleaning and removing impurities, 100g of bagasse is mixed with 40g of liquid water-based acrylic resin and impregnated for 2 hours, and then rolled with a gear-type rolling mill. The rolled material is in the form of scattered materials;
[0048] 2. Carbonization: Put the rolling material into a heating tank, fill it with argon to discharge the air, heat it to 625°C, keep it warm for 6 hours, and after cooling down naturally, complete the carbonization step to obtain carbonized material;
[0049] 3. Activation: Put the carbonized material in the previous step into a vacuum tank, raise the temperature of the carbonized material to 70°C, vacuumize, inject a sodium hydroxide solution with a mass percentage concentration of 70% to soak, and then put the carbonized material into the heating tank after drying , fill up with argon to remove the air, raise the temperature to 780°C, keep it warm for 2 hours, and obtain the activated material after natural cooli...
Embodiment 2
[0052] 1. Rolling: After cleaning and removing 100g of straw stalk slag, mixed with 100g of liquid water-based melamine-formaldehyde resin and end-capped acid catalyst and impregnated for 4 hours, rolling is carried out with a gear and smooth roll rolling mill, and the rolling material produced by rolling is The form is a flat sheet material;
[0053] 2. Carbonization: put the rolling material into a heating tank, fill it up with nitrogen gas to discharge the air, heat it to 600°C, keep it warm for 4 hours, and complete the carbonization step after natural cooling to obtain carbonized material;
[0054] 3. Activation: Put the carbonized material in the previous step into a vacuum tank, raise the temperature of the carbonized material to 70°C, vacuumize, inject a potassium hydroxide solution with a mass percentage concentration of 60% for soaking, and put the carbonized material into the heating tank after drying , fill up with argon to remove the air, raise the temperature to ...
PUM
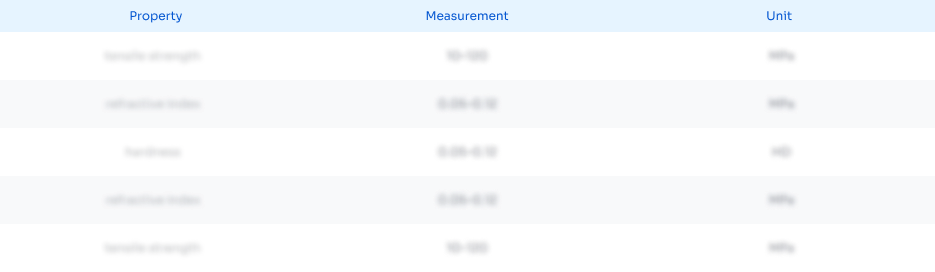
Abstract
Description
Claims
Application Information

- R&D
- Intellectual Property
- Life Sciences
- Materials
- Tech Scout
- Unparalleled Data Quality
- Higher Quality Content
- 60% Fewer Hallucinations
Browse by: Latest US Patents, China's latest patents, Technical Efficacy Thesaurus, Application Domain, Technology Topic, Popular Technical Reports.
© 2025 PatSnap. All rights reserved.Legal|Privacy policy|Modern Slavery Act Transparency Statement|Sitemap|About US| Contact US: help@patsnap.com