Modularized direct torque control rehabilitation robot joint
A rehabilitation robot and torque control technology, applied in the direction of joints, manipulators, manufacturing tools, etc., can solve the problems of not considering the importance of joint feedback information, low joint transmission accuracy of rehabilitation robots, lack of mechanical positioning design, etc., to improve accuracy and reliability. The effect of versatility, light weight and high output torque
- Summary
- Abstract
- Description
- Claims
- Application Information
AI Technical Summary
Problems solved by technology
Method used
Image
Examples
Embodiment Construction
[0028] In the following description, for purposes of explanation, numerous specific details are set forth in order to provide a thorough understanding of one or more embodiments. It may be evident, however, that these embodiments may be practiced without these specific details. In other instances, well-known structures and devices are shown in block diagram form in order to facilitate describing one or more embodiments.
[0029] figure 1 The exploded structure of a joint of a modular direct torque control rehabilitation robot according to an embodiment of the present invention is shown.
[0030] Such as figure 1 As shown, the modular direct torque control rehabilitation robot joint provided by the embodiment of the present invention includes a left end cover 1, a harmonic reducer 2, a DC three-phase brushless motor 3, a joint mechanical limiter 4, an absolute encoder 5, and a circuit Plate 6, shell 7, right end cover 8 and electromagnetic brake 9, the left end cover 1 is in...
PUM
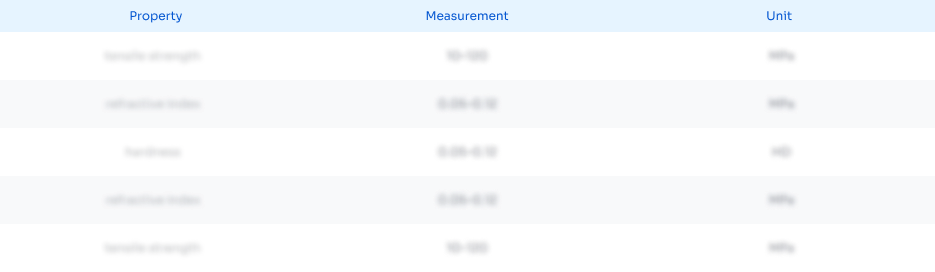
Abstract
Description
Claims
Application Information

- Generate Ideas
- Intellectual Property
- Life Sciences
- Materials
- Tech Scout
- Unparalleled Data Quality
- Higher Quality Content
- 60% Fewer Hallucinations
Browse by: Latest US Patents, China's latest patents, Technical Efficacy Thesaurus, Application Domain, Technology Topic, Popular Technical Reports.
© 2025 PatSnap. All rights reserved.Legal|Privacy policy|Modern Slavery Act Transparency Statement|Sitemap|About US| Contact US: help@patsnap.com