2024 aluminum alloy melting casting method
An aluminum alloy and smelting furnace technology, applied in the field of aluminum alloy, can solve problems such as improper process selection and cracks, and achieve the effects of reducing production costs, fewer defects, and reducing losses
- Summary
- Abstract
- Description
- Claims
- Application Information
AI Technical Summary
Problems solved by technology
Method used
Image
Examples
Embodiment 1
[0033] Such as figure 1 A 2024 aluminum alloy smelting and casting method is shown, comprising the steps of:
[0034] A. Ingredients: The mass percentage ratio of each element in the 2024 aluminum alloy ingot raw material is as follows:
[0035]
[0036]
[0037] Prepare aluminum alloy raw materials according to the above ratio;
[0038] B. Smelting: In the smelting process, the electrolytic aluminum liquid and other alloy solid materials are first added to the smelting furnace to stir and melt, and the temperature after melting is ≤760°C, and then the aluminum-copper master alloy, pure zinc ingot, and aluminum-zirconium master alloy are put into smelting Stir and melt in the furnace, the melting temperature is 750±5°C, and then put the aluminum-titanium master alloy and pure magnesium ingot into the melting furnace with a magnesium feeder for stirring and melting, the melting temperature is 740±5°C, after complete melting The molten aluminum alloy is evenly stirred by...
Embodiment 2
[0044] The difference between embodiment 2 and embodiment 1 is that the mass percentage ratio of each element in the 2024 aluminum alloy ingot raw material in step A is as follows:
[0045] element
Embodiment 3
[0047] The difference between Example 3 and Example 1 is that the mass percentage ratio of each element in the 2024 aluminum alloy ingot raw material in step A is as follows:
[0048]
[0049]
PUM
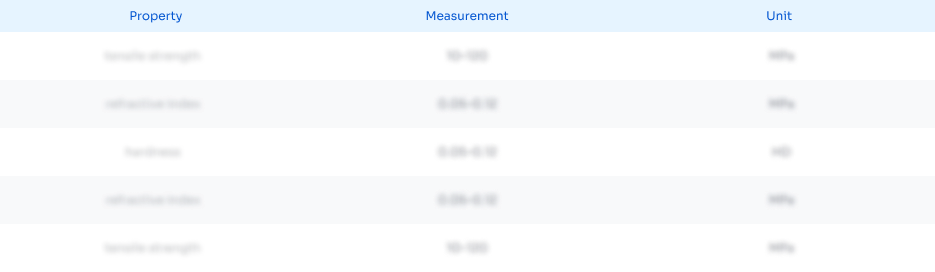
Abstract
Description
Claims
Application Information

- R&D
- Intellectual Property
- Life Sciences
- Materials
- Tech Scout
- Unparalleled Data Quality
- Higher Quality Content
- 60% Fewer Hallucinations
Browse by: Latest US Patents, China's latest patents, Technical Efficacy Thesaurus, Application Domain, Technology Topic, Popular Technical Reports.
© 2025 PatSnap. All rights reserved.Legal|Privacy policy|Modern Slavery Act Transparency Statement|Sitemap|About US| Contact US: help@patsnap.com