Water-based coating for preventing casting veins and preparation method thereof
A water-based coating and veining technology, which is applied to casting molding equipment, coatings, casting molds, etc., can solve the problems of cumbersome manufacturing process, high production cost, time-consuming and laborious, etc., and achieve high reactivity, lower surface temperature, penetration strong effect
- Summary
- Abstract
- Description
- Claims
- Application Information
AI Technical Summary
Problems solved by technology
Method used
Image
Examples
Embodiment 1
[0021] (1) Start the disperser, set the speed at 600r / min, pour 23Kg of clean water into the dispersion kettle, then pour 8Kg of magnesium aluminum silicate into the dispersion kettle, and adjust the speed of the disperser to 1500r after dispersing for 5 minutes / min, disperse at 1500r / min for 15min, take it out, and let it age for 24h to obtain pretreated magnesium aluminum silicate.
[0022] (2) Add pretreated magnesium aluminum silicate and 10Kg of nano-aluminum sol into the ball mill, start the ball mill after sealing, and run at a speed of 200r / min for 6 hours to obtain a nano-powder slurry with strong thixotropy.
[0023] (3) Pour the nano powder slurry and 23Kg of clean water into the dispersing kettle, start the dispersing machine, set the speed at 600r / min, add 8Kg of iron red powder, 20Kg of mica powder and 10Kg of aluminum silicate fiber in sequence , after the feeding is completed, adjust the rotating speed to 1400r / min, disperse for 15min, and obtain the coating. ...
Embodiment 2
[0025] (1) Start the disperser, set the speed at 600r / min, pour 20Kg of clean water into the dispersion kettle, then pour 6Kg of magnesium aluminum silicate into the dispersion kettle, and adjust the speed of the disperser to 1500r after dispersing for 5 minutes / min, disperse at 1500r / min for 15min, take it out, and let it age for 24h to obtain pretreated magnesium aluminum silicate.
[0026] (2) Add pretreated magnesium aluminum silicate and 12Kg of nano-aluminum sol into the ball mill, start the ball mill after sealing, run at a speed of 200r / min for 6h, and obtain a nano-powder slurry with strong thixotropy.
[0027] (3) Pour the nano powder slurry and 20Kg of clean water into the dispersing kettle, start the dispersing machine, set the speed at 600r / min, add 5Kg of iron red powder, 22Kg of mica powder and 15Kg of aluminum silicate fiber in sequence , after the feeding is completed, adjust the rotating speed to 1400r / min, disperse for 15min, and obtain the coating.
Embodiment 3
[0029] (1) Start the disperser, set the speed at 600r / min, pour 20Kg of clean water into the dispersion kettle, then pour 6Kg of magnesium aluminum silicate into the dispersion kettle, and adjust the speed of the disperser to 1500r after dispersing for 5 minutes / min, disperse at 1500r / min for 15min, take it out, and let it age for 24h to obtain pretreated magnesium aluminum silicate.
[0030] (2) Add pretreated magnesium aluminum silicate and 10Kg of nano-aluminum sol into the ball mill, start the ball mill after sealing, run at a speed of 200r / min for 6h, and obtain a nano-powder slurry with strong thixotropy.
[0031] (3) Pour the nano powder slurry and 20Kg of clean water into the dispersing kettle, start the dispersing machine, set the speed at 600r / min, add 7Kg of iron red powder, 25Kg of mica powder and 12Kg of aluminum silicate fiber in sequence , after the feeding is completed, adjust the rotating speed to 1400r / min, disperse for 15min, and obtain the coating.
PUM
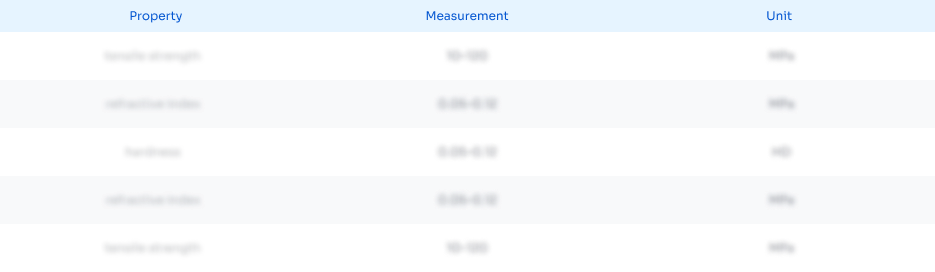
Abstract
Description
Claims
Application Information

- R&D Engineer
- R&D Manager
- IP Professional
- Industry Leading Data Capabilities
- Powerful AI technology
- Patent DNA Extraction
Browse by: Latest US Patents, China's latest patents, Technical Efficacy Thesaurus, Application Domain, Technology Topic, Popular Technical Reports.
© 2024 PatSnap. All rights reserved.Legal|Privacy policy|Modern Slavery Act Transparency Statement|Sitemap|About US| Contact US: help@patsnap.com