Corrosion-resisting tensile type alloy steel and production technology thereof
A tensile and corrosion-resistant technology, applied in the field of metal smelting, can solve the problems of poor corrosion resistance of steel, poor steel plasticity, short service life, etc., and achieve excellent wear resistance, increased strength and hardness, and strong wear resistance Effect
- Summary
- Abstract
- Description
- Claims
- Application Information
AI Technical Summary
Problems solved by technology
Method used
Examples
Embodiment 1
[0023] A corrosion-resistant and tensile-resistant alloy steel provided in this embodiment has the following mass percentages of chemical composition: C: 0.22%, Cr: 4.36%, Al: 0.71%, Zn: 0.33%, Cu: 0.41%, Ti: 0.45%, Si: 0.11%, W: 0.12%, Nb: 0.12%, Mn: 0.14%, and the balance is Fe and unavoidable impurities.
[0024] The preparation method of a corrosion-resistant and tensile-resistant alloy steel provided in this embodiment includes the following steps: S1: Add each raw material into a melting furnace according to the mass percentage, adjust the temperature of the melting furnace to 1580° C., and melt for 1 hour. The raw materials are smelted into an alloy solution, and the alloy solution is desulfurized and deoxidized, and then a refining agent is added for refining and slag removal;
[0025] S2: The alloy solution is poured into the ladle, and the alloy solution in the ladle is micro-alloyed with rare earth alloy magnesium. After the treatment, the alloy solution is poured i...
Embodiment 2
[0030] A corrosion-resistant and tensile-resistant alloy steel provided in this embodiment has the following mass percentages of chemical composition: C: 0.31%, Cr: 5.24%, Al: 0.74%, Zn: 0.46%, Cu: 0.58%, Ti: 0.49%, Si: 0.19%, W: 0.15%, Nb: 0.14%, Mn: 0.17%, and the balance is Fe and unavoidable impurities.
[0031] A method for preparing a corrosion-resistant and tensile-resistant alloy steel provided in this embodiment includes the following steps: S1: Add each raw material into a melting furnace according to the mass percentage, adjust the temperature of the melting furnace to 1680° C., and melt for 2 hours. The raw materials are smelted into an alloy solution, and the alloy solution is desulfurized and deoxidized, and then a refining agent is added for refining and slag removal;
[0032] S2: The alloy solution is poured into the ladle, and the alloy solution in the ladle is micro-alloyed with rare earth alloy magnesium. After the treatment, the alloy solution is poured int...
Embodiment 3
[0037] A corrosion-resistant and tensile-resistant alloy steel provided in this embodiment has the following mass percentages of chemical composition: C: 0.26%, Cr: 4.79%, Al: 0.73%, Zn: 0.39%, Cu: 0.49%, Ti: 0.47%, Si: 0.15%, W: 0.14%, Nb: 0.13%, Mn: 0.16%, and the balance is Fe and unavoidable impurities.
[0038] The preparation method of a corrosion-resistant and tensile-resistant alloy steel provided in this embodiment includes the following steps: S1: Add each raw material into a melting furnace according to the mass percentage, adjust the temperature of the melting furnace to 1630° C., and melt for 1.5 hours. The raw materials are smelted into an alloy solution, and the alloy solution is desulfurized and deoxidized, and then a refining agent is added for refining and slag removal;
[0039] S2: The alloy solution is poured into the ladle, and the alloy solution in the ladle is micro-alloyed with rare earth alloy magnesium. After the treatment, the alloy solution is poure...
PUM
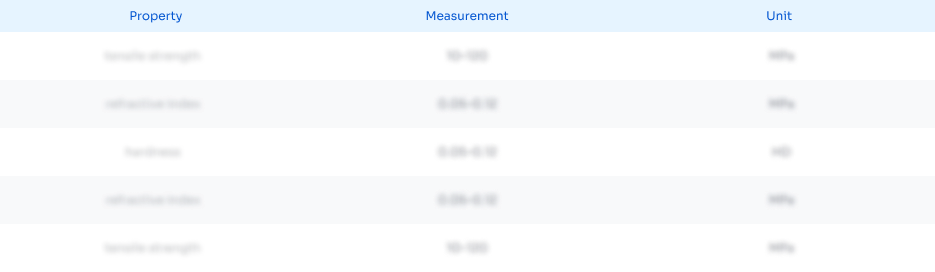
Abstract
Description
Claims
Application Information

- R&D
- Intellectual Property
- Life Sciences
- Materials
- Tech Scout
- Unparalleled Data Quality
- Higher Quality Content
- 60% Fewer Hallucinations
Browse by: Latest US Patents, China's latest patents, Technical Efficacy Thesaurus, Application Domain, Technology Topic, Popular Technical Reports.
© 2025 PatSnap. All rights reserved.Legal|Privacy policy|Modern Slavery Act Transparency Statement|Sitemap|About US| Contact US: help@patsnap.com