Polyurethane composition for car steering wheel and preparation method of polyurethane composition
A steering wheel and polyurethane technology, applied in the field of polyurethane, can solve problems such as easy sweat absorption and poor hand feeling, and achieve the effects of reducing environmental hazards, scientific and reasonable preparation methods, and wide adaptability
- Summary
- Abstract
- Description
- Claims
- Application Information
AI Technical Summary
Problems solved by technology
Method used
Image
Examples
Embodiment 1
[0036] Component A is made from the following raw materials in parts by weight:
[0037]
[0038] Component B is made from the following raw materials in parts by weight:
[0039]
[0040] The preparation method is as follows:
[0041] Component A: Put polyether polyol KE-810 and polyether ester polyol INOVOL 2000T into the reaction kettle and stir, then add foam stabilizer EPK-127, catalyst DABCO BL-11, catalyst DABCO NE1060, and chain extender in sequence BDO, chain extender EG, foaming agent H 2 O, opening agent GK-350D and sodium hydroxide nanofibers. At room temperature, the rotation speed is 50 rpm, and the mixture is stirred for 1 hour to obtain the product of component A.
[0042] Component B: Put the polyether polyol 10LD83E into the reaction kettle at room temperature, stir and dehydrate and degas for 2 hours under vacuum (≤-0.098MPa) at 90°C, then cool down to 40°C, add propylene glycol DPG first, and then add isocyanate 0129M and pure MDI44C, raise the te...
Embodiment 2
[0046] Component A is made from the following raw materials in parts by weight:
[0047]
[0048] Component B is made from the following raw materials in parts by weight:
[0049]
[0050] The preparation method is as follows:
[0051] Component A: Put polyether polyol KE-810 and polyether ester polyol INOVOL 2000T into the reaction kettle and stir, then add foam stabilizer EPK-127, catalyst DABCO BL-11, catalyst DABCO NE1060, and chain extender in sequence BDO, chain extender EG, foaming agent H 2 O, opening agent GK-350D and sodium hydroxide nanofibers. At room temperature, the rotation speed is 75 rpm, and stirred for 1 hour to obtain the product of component A.
[0052] Component B: Put the polyether polyol 10LD83E into the reaction kettle at room temperature, stir and dehydrate and degas for 2 hours under vacuum (≤-0.098MPa) at 90°C, then cool down to 40°C, add propylene glycol DPG first, and then add isocyanate 0129M and pure MDI44C, heat up to 80°C for 2 hours...
Embodiment 3
[0056] Component A is made from the following raw materials in parts by weight:
[0057]
[0058] Component B is made from the following raw materials in parts by weight:
[0059]
[0060] The preparation method is as follows:
[0061] Component A: Put polyether polyol KE-810 and polyether ester polyol INOVOL 2000T into the reaction kettle and stir, then add foam stabilizer EPK-127, catalyst DABCO BL-11, catalyst DABCO NE1060, and chain extender in sequence BDO, chain extender EG, foaming agent H 2 O, opening agent GK-350D and sodium hydroxide nanofibers. At room temperature, the rotation speed is 80 rpm, and the mixture is stirred for 1 hour to obtain the product of component A.
[0062] Component B: Put the polyether polyol 10LD83E into the reaction kettle at room temperature, stir and dehydrate and degas for 2 hours under vacuum (≤-0.098MPa) at 90°C, then cool down to 40°C, add propylene glycol DPG first, and then add isocyanate 0129M and pure MDI44C, raise the temp...
PUM
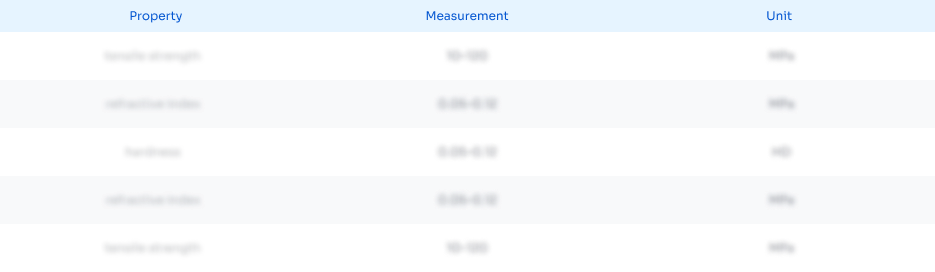
Abstract
Description
Claims
Application Information

- R&D Engineer
- R&D Manager
- IP Professional
- Industry Leading Data Capabilities
- Powerful AI technology
- Patent DNA Extraction
Browse by: Latest US Patents, China's latest patents, Technical Efficacy Thesaurus, Application Domain, Technology Topic, Popular Technical Reports.
© 2024 PatSnap. All rights reserved.Legal|Privacy policy|Modern Slavery Act Transparency Statement|Sitemap|About US| Contact US: help@patsnap.com