Nondestructive inspection and performance prediction method for composite structures, ultrasonic wave imaging system and calibration method
A technology for inspecting systems and composite structures, applied in the analysis of solids using sound waves/ultrasonic waves/infrasonic waves, material analysis using sound waves/ultrasonic waves/infrasonic waves, and testing composite materials, etc., which can solve time-consuming and expensive work and other problems
- Summary
- Abstract
- Description
- Claims
- Application Information
AI Technical Summary
Problems solved by technology
Method used
Image
Examples
Embodiment Construction
[0029] For purposes of illustration, systems and methods for the non-destructive inspection of structures made of composite materials (e.g., composite layered structures made of fiber-reinforced plastics) that enable the identification and quantification of composite Wrinkles in structures and predicting performance. However, not all features of an actual implementation are described in this specification. Those skilled in the art will recognize that in the development of any such embodiment, many implementation-specific decisions must be made in order to achieve the developer's specific goals, such as compliance with system-related and business-related constraints , the constraints of one implementation will be different from those of another implementation. Moreover, it will be appreciated that such a development effort might be complex and time consuming, but would nevertheless be a routine undertaking of those of ordinary skill in the art having the benefit of this disclo...
PUM
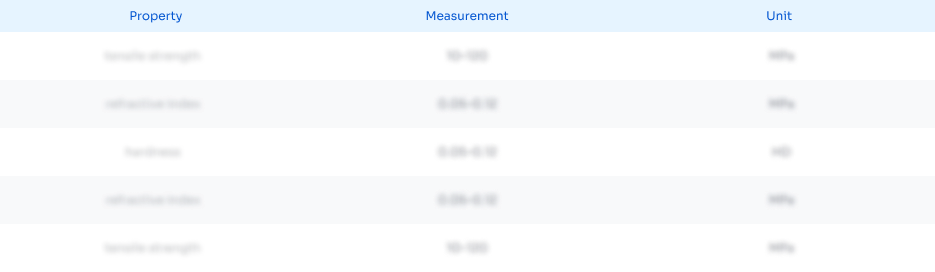
Abstract
Description
Claims
Application Information

- Generate Ideas
- Intellectual Property
- Life Sciences
- Materials
- Tech Scout
- Unparalleled Data Quality
- Higher Quality Content
- 60% Fewer Hallucinations
Browse by: Latest US Patents, China's latest patents, Technical Efficacy Thesaurus, Application Domain, Technology Topic, Popular Technical Reports.
© 2025 PatSnap. All rights reserved.Legal|Privacy policy|Modern Slavery Act Transparency Statement|Sitemap|About US| Contact US: help@patsnap.com