Coal pyrolysis system and method
A coal pyrolysis and pyrolysis technology, applied in the field of coal pyrolysis systems, can solve the problems of unrecyclable materials, waste of resources, and large amounts of water resources, and achieve good water-saving effects, small footprint, and high resource utilization. Effect
- Summary
- Abstract
- Description
- Claims
- Application Information
AI Technical Summary
Problems solved by technology
Method used
Image
Examples
Embodiment Construction
[0041] Embodiments of the present invention are described in detail below, and examples of the embodiments are shown in the drawings, wherein the same or similar reference numerals denote the same or similar elements or elements having the same or similar functions throughout. The embodiments described below by referring to the figures are exemplary only for explaining the present invention and should not be construed as limiting the present invention.
[0042] The coal pyrolysis system according to the present invention generally includes a pyrolysis unit, a coke quenching unit, a waste heat recovery unit, a dust removal and purification unit, and an oil-water separation and purification unit. Among them, the pyrolysis unit, the shown coke quenching unit, the shown waste heat recovery unit, and the shown dust removal and purification unit are connected in sequence, and the oil-water separation and purification unit is connected with the pyrolysis unit for oil-water separation ...
PUM
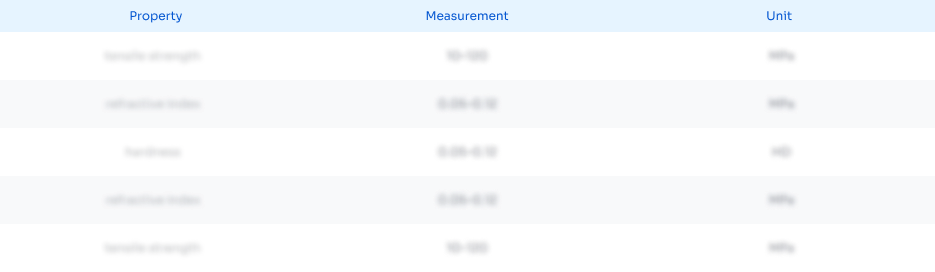
Abstract
Description
Claims
Application Information

- R&D
- Intellectual Property
- Life Sciences
- Materials
- Tech Scout
- Unparalleled Data Quality
- Higher Quality Content
- 60% Fewer Hallucinations
Browse by: Latest US Patents, China's latest patents, Technical Efficacy Thesaurus, Application Domain, Technology Topic, Popular Technical Reports.
© 2025 PatSnap. All rights reserved.Legal|Privacy policy|Modern Slavery Act Transparency Statement|Sitemap|About US| Contact US: help@patsnap.com