Method for preparing ethylene sulfate by using microchannel reactor
A microchannel reactor, vinyl sulfate technology, applied in the direction of organic chemistry, etc., can solve the problems of poor temperature control effect, low production capacity per unit time, and long mixing and dissolving time in the single-pot reaction, so as to shorten the production cycle and have no amplification effect. , beneficial to industrial applications
- Summary
- Abstract
- Description
- Claims
- Application Information
AI Technical Summary
Problems solved by technology
Method used
Image
Examples
Embodiment 1
[0024]Raw material preparation: sodium hypochlorite solution: the mass concentration is 13%, and the mass is 689g. Dichloromethane solution of vinyl sulfite: Dissolve 108g of vinyl sulfite in 1200g of dichloromethane at room temperature, and keep stirring to configure, with a mass concentration of 9%. Sodium bicarbonate solution: Dissolve 84g of sodium bicarbonate in 1120g of deionized water at room temperature and stir continuously, with a mass concentration of 7%. Ruthenium trichloride solution: prepared by dissolving 0.78g of ruthenium trichloride in 48g of deionized water at room temperature, stirring continuously, with a mass concentration of 1.6%. The molar ratio of vinyl sulfite to sodium hypochlorite is 1:1.2, and the molar ratio of ruthenium trichloride to vinyl sulfite is 0.03%.
[0025] The preparation process is as follows: set the temperature of the temperature control tank 1 at -10 to 10°C, prepare the prepared dichloromethane solution of vinyl sulfite with a ma...
Embodiment 2
[0027] Raw material preparation: sodium hypochlorite solution: the mass concentration is 13%, and the mass is 687g. Dichloromethane solution of vinyl sulfite: Dissolve 108g of vinyl sulfite in 1200g of dichloromethane at room temperature, and keep stirring to configure, with a mass concentration of 9%. Sodium bicarbonate solution: Dissolve 84g of sodium bicarbonate in 1120g of deionized water at room temperature and stir continuously, with a mass concentration of 7%. Ruthenium trichloride solution: prepared by dissolving 0.78g of ruthenium trichloride in 48g of deionized water at room temperature, stirring continuously, with a mass concentration of 1.6%. The molar ratio of vinyl sulfite to sodium hypochlorite is 1:1.2, and the molar ratio of ruthenium trichloride to vinyl sulfite is 0.03%.
[0028] The preparation process is as follows: set the temperature of the temperature control tank 1 at -10 to 10°C, prepare the prepared dichloromethane solution of vinyl sulfite with a m...
Embodiment 3
[0030] Raw material preparation: sodium hypochlorite solution: the mass concentration is 13%, and the mass is 687g. Dichloromethane solution of vinyl sulfite: Dissolve 108g of vinyl sulfite in 1200g of dichloromethane at room temperature, and keep stirring to configure, with a mass concentration of 9%. Sodium bicarbonate solution: Dissolve 84g of sodium bicarbonate in 1120g of deionized water at room temperature and stir continuously, with a mass concentration of 7%. Ruthenium trichloride solution: prepared by dissolving 0.78g of ruthenium trichloride in 48g of deionized water at room temperature, stirring continuously, with a mass concentration of 1.6%. The molar ratio of vinyl sulfite to sodium hypochlorite is 1:1.2, and the molar ratio of ruthenium trichloride to vinyl sulfite is 0.03%.
[0031] The preparation process is as follows: set the temperature of the temperature control tank 1 at -20 to 20°C, prepare the prepared dichloromethane solution of vinyl sulfite with a m...
PUM
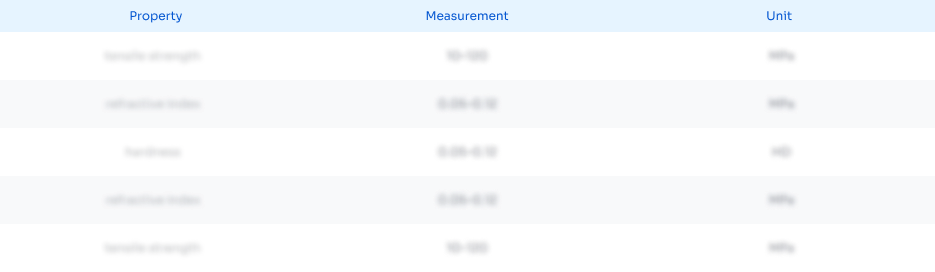
Abstract
Description
Claims
Application Information

- R&D Engineer
- R&D Manager
- IP Professional
- Industry Leading Data Capabilities
- Powerful AI technology
- Patent DNA Extraction
Browse by: Latest US Patents, China's latest patents, Technical Efficacy Thesaurus, Application Domain, Technology Topic, Popular Technical Reports.
© 2024 PatSnap. All rights reserved.Legal|Privacy policy|Modern Slavery Act Transparency Statement|Sitemap|About US| Contact US: help@patsnap.com