Steel-aluminium transition joint T-shaped bilateral space welding process numerical simulation calculation method
A transition joint and welding process technology, which is applied in the field of numerical simulation calculation of T-shaped double-sided interval welding process of steel-aluminum transition joint, can solve problems such as cracking failure, steel-aluminum interface temperature prediction, and interface performance degradation
- Summary
- Abstract
- Description
- Claims
- Application Information
AI Technical Summary
Problems solved by technology
Method used
Image
Examples
specific Embodiment approach
[0044] Step 1: Establish a three-dimensional (or two-dimensional) thermal-mechanical coupling calculation model for the welding process of steel-aluminum transition joints
[0045] Establish the overall geometric model of three-dimensional parts (or two-dimensional cross-sections) in general finite element software, including steel-aluminum transition joints, welds, welded aluminum plates and steel plates to be welded and other parts, and combine different parts separately or Contact setting and assembly constitute the overall geometric model; then set the thermophysical parameters of steel, pure aluminum and aluminum alloy materials that change with temperature, and assign material properties to the corresponding structural parts; finally, the overall parts are meshed, and the 3D model adopts hexahedron Element mesh (tetrahedral element mesh is used for 2D cross-section model), and the mesh near the weld position is subdivided.
[0046] Step 2: Set the initial conditions and ...
PUM
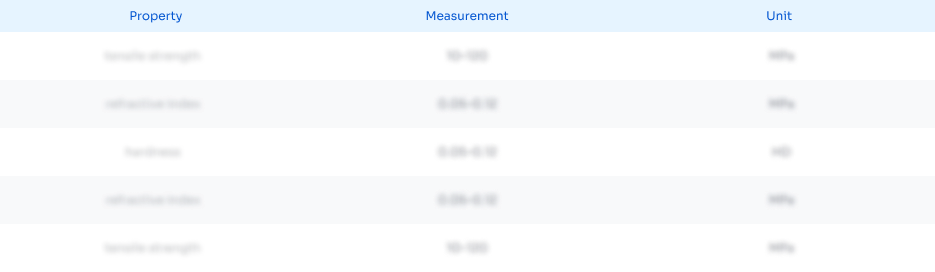
Abstract
Description
Claims
Application Information

- R&D
- Intellectual Property
- Life Sciences
- Materials
- Tech Scout
- Unparalleled Data Quality
- Higher Quality Content
- 60% Fewer Hallucinations
Browse by: Latest US Patents, China's latest patents, Technical Efficacy Thesaurus, Application Domain, Technology Topic, Popular Technical Reports.
© 2025 PatSnap. All rights reserved.Legal|Privacy policy|Modern Slavery Act Transparency Statement|Sitemap|About US| Contact US: help@patsnap.com