Injection molded control panel and injection molding process thereof
A control panel and injection molding technology, which can be applied to other household appliances, household components, applications, etc., can solve the problems of flammability, increased product weight, weak insulation, etc., to improve wear resistance and fatigue resistance, and injection molding process operation Convenience, effect of improving aging resistance
- Summary
- Abstract
- Description
- Claims
- Application Information
AI Technical Summary
Problems solved by technology
Method used
Examples
Embodiment 1
[0031] An injection molding control panel, which is made of the following raw materials in parts by weight: 45 parts of PC resin flakes, 7 parts of panel filler, 5 parts of powdered metal, and 1 part of rare earth organic complex type light converting agent.
[0032] The panel filler includes four raw materials of calcium silicate, magnesium carbonate, diatom mud and glass fiber, and the panel filler is mixed with calcium silicate, magnesium carbonate, diatom mud and glass fiber in a mass ratio of 1:0.5:0.3:1 After drying, crushing, pulverizing, and passing through a 500-mesh sieve, it is obtained.
[0033] The powdered metal is a mixture of chromium and zinc, and the particle size of the powdered metal is 30um.
[0034] An injection molding process for an injection molding control panel, comprising the steps of:
[0035] (1) Raw material pretreatment: wash the PC resin flakes with ethanol for 3 times and then place them in an oven to dry. After completion, put them into a cr...
Embodiment 2
[0045] An injection molding control panel is made of the following raw materials in parts by weight: 50 parts of PC resin flakes, 9 parts of panel filler, 7 parts of powdered metal, and 1.5 parts of rare earth inorganic compound light converting agent.
[0046] The panel filler includes four raw materials of calcium silicate, magnesium carbonate, diatom mud and glass fiber, and the panel filler is mixed with calcium silicate, magnesium carbonate, diatom mud and glass fiber in a mass ratio of 1:0.6:0.5:1.2 After drying, crushing, pulverizing, and passing through a 500-mesh sieve, it is obtained.
[0047] The powdered metal is one of chromium, zinc, titanium and nickel alone or a mixture of two or more, and the particle size of the powdered metal is 35um.
[0048] An injection molding process for an injection molding control panel, comprising the steps of:
[0049] (1) Raw material pretreatment: wash the PC resin flakes with ethanol for 4 times and then place them in an oven to...
Embodiment 3
[0059] An injection molded control panel, which is made of the following raw materials in parts by weight: 55 parts of PC resin flakes, 11 parts of panel filler, 8 parts of powdered metal, and 2 parts of rare earth organic complex light converting agent.
[0060] The panel filler includes four raw materials of calcium silicate, magnesium carbonate, diatom mud and glass fiber, and the panel filler is mixed with calcium silicate, magnesium carbonate, diatom mud and glass fiber in a mass ratio of 1:0.7:0.6:1.5 After drying, crushing, pulverizing, and passing through a 500-mesh sieve, it is obtained.
[0061] The powdered metal is one of chromium, zinc, titanium and nickel alone or a mixture of two or more, and the particle size of the powdered metal is 40um.
[0062] An injection molding process for an injection molding control panel, comprising the steps of:
[0063] (1) Raw material pretreatment: wash the PC resin flakes with ethanol for 5 times and then place them in an oven ...
PUM
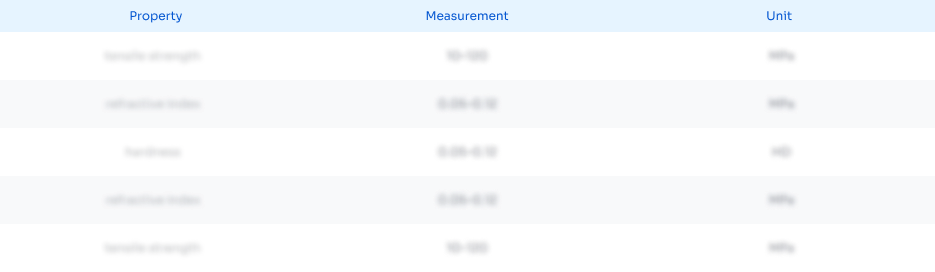
Abstract
Description
Claims
Application Information

- R&D Engineer
- R&D Manager
- IP Professional
- Industry Leading Data Capabilities
- Powerful AI technology
- Patent DNA Extraction
Browse by: Latest US Patents, China's latest patents, Technical Efficacy Thesaurus, Application Domain, Technology Topic, Popular Technical Reports.
© 2024 PatSnap. All rights reserved.Legal|Privacy policy|Modern Slavery Act Transparency Statement|Sitemap|About US| Contact US: help@patsnap.com