Method for machining of aluminum alloy hub flange face
一种铝合金轮毂、法兰面的技术,应用在金属加工设备、用于车床的刀具、轮毂等方向,能够解决车削量过大、车削量大、影响人身安全等问题,达到减小进给率、保证能力强、减小车削量的效果
- Summary
- Abstract
- Description
- Claims
- Application Information
AI Technical Summary
Problems solved by technology
Method used
Image
Examples
Embodiment 1
[0017] Flange turning four times, when using 120°R3 boring tool for rough turning, the forward rotation speed of the wheel hub is set to 1200r / min, the roughing feed rate is 0.40mm / r, and the turning amount on each side is 1mm; use 95°cutter for fine turning When the wheel hub forward speed is set to 1200r / min, the feed rate of the first pass of finishing turning is 0.15mm / r, the turning amount is 0.35mm, the second feeding rate of finishing turning is 0.1mm / r, and the turning amount is 0.05mm.
Embodiment 2
[0019] Flange turning four times, when using 120°R3 boring tool for rough turning, the wheel hub forward speed is set to 1400r / min, the roughing feed rate is 0.45mm / r, and the turning amount on each side is 1mm; use 95°cutter for fine turning When the wheel hub forward speed is set to 1300r / min, the feed rate of the first pass of fine turning is 0.18mm / r, the turning amount is 0.35mm, the feed rate of the second pass of fine turning is 0.11mm / r, and the turning amount is 0.05mm.
Embodiment 3
[0021] Flange turning four times, when using 120°R3 boring tool for rough turning, the wheel hub forward speed is set to 1500r / min, the rough turning feed rate is 0.5mm / r, and the turning amount on each side is 1mm; use 95°cutter for fine turning When the wheel hub forward speed is set to 1500r / min, the feed rate of the first pass of fine turning is 0.2mm / r, the turning amount is 0.35mm, the feed rate of the second pass of fine turning is 0.12mm / r, and the turning amount is 0.05mm.
PUM
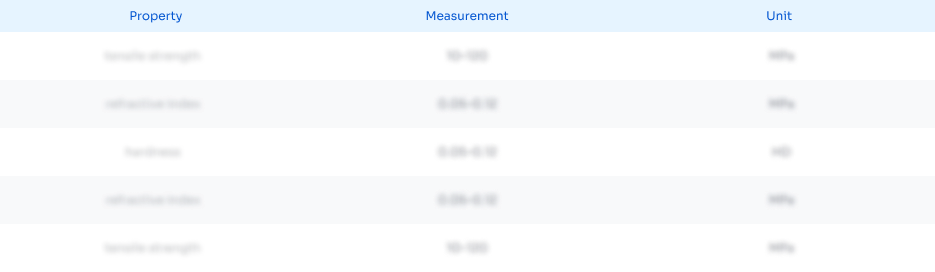
Abstract
Description
Claims
Application Information

- R&D
- Intellectual Property
- Life Sciences
- Materials
- Tech Scout
- Unparalleled Data Quality
- Higher Quality Content
- 60% Fewer Hallucinations
Browse by: Latest US Patents, China's latest patents, Technical Efficacy Thesaurus, Application Domain, Technology Topic, Popular Technical Reports.
© 2025 PatSnap. All rights reserved.Legal|Privacy policy|Modern Slavery Act Transparency Statement|Sitemap|About US| Contact US: help@patsnap.com