Pre-film cleaning treatment method of circulating water system
A technology of circulating water system and treatment method, which is applied in oxidation water/sewage treatment, metal material coating process, etc., to achieve the effects of reducing sewage discharge, reducing sewage treatment costs, and saving manpower and material resources
- Summary
- Abstract
- Description
- Claims
- Application Information
AI Technical Summary
Problems solved by technology
Method used
Examples
example 1
[0015] Example 1, in May 2016, an oil refinery in Shandong kept 2000m of water 3 , circulation capacity 6000m 3 / h, the plant's fourth circulating water plant system was put into use in 2006, and the cleaning and pre-membrane work is carried out once a year. The plant uses groundwater as supplementary water, and its water quality is negative hard water, with calcium ions lower than 30mg / L (calculated as calcium carbonate) and alkalinity 400mg / L (calculated as calcium carbonate).
[0016] The pre-membrane cleaning process of the present invention: peeling and cleaning stage: without affecting production, open all valves and open the pump to the maximum flow rate. Maintain a certain liquid level and add 100kg of trichloroisocyanuric acid, while detecting the turbidity and iron ions in the water. After 4 hours of operation, 200kg of dodecyldimethylbenzyl ammonium chloride was added, and after 2 hours, the detected turbidity rose to 50mg / L and the iron ion was 3.8mg / L.
[0017]...
example 2
[0019] Example 2 In November 2015, a coking plant in Hebei kept 3000m of water 3 , circulation volume 8000m 3 / h, the equipment of the circulating water plant includes methanol, chemical products, thermal power, etc. The methanol system often leaks organic matter into the circulating water system, which leads to serious bacterial growth, so the cleaning of the pre-membrane is performed once a year. The alkalinity and hardness of the water quality are moderate, but the dust is relatively large due to the coal yard, which has a certain impact on the turbidity of the circulating water.
[0020] Stripping and cleaning stage: without affecting production, open all valves and pump to maximum flow rate.
[0021] Maintain a certain liquid level and add 300kg of oxidizing bactericide sodium hypochlorite to run, and detect the turbidity and iron ions in the water at the same time. After 6 hours of operation, 600kg of slime stripping agent dodecyl dimethyl benzyl ammonium chloride was...
example 3
[0024] Example 3 In August 2015, a coking plant in Shanxi kept 3000m of water 3 , circulation capacity 7000m 3 / h, the equipment of the circulating water plant includes chemical production, refrigeration, thermoelectricity, etc. The water quality is typical high-hard and high-alkali water. The coal yard has a lot of dust and is located in an area with severe water shortage. Therefore, the cleaning of the pre-membrane is carried out every two years.
[0025] Stripping and cleaning stage: without affecting production, open all valves and pump to maximum flow rate. Keep a certain liquid level and add 300kg of trichloroisocyanuric acid to run, and detect the turbidity, iron ion and calcium ion in the water at the same time. After 4 hours, 600kg of dodecylbenzyl ammonium chloride was added, and after 2 hours, the detected turbidity rose to 100mg / L, iron ions 2.5mg / L, and calcium ions 500mg / L.
[0026] After 6 hours, enter the rust removal and pre-film stage, add urotropine 300kg...
PUM
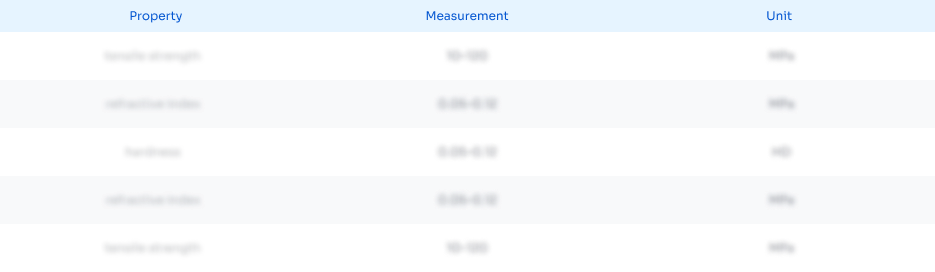
Abstract
Description
Claims
Application Information

- R&D Engineer
- R&D Manager
- IP Professional
- Industry Leading Data Capabilities
- Powerful AI technology
- Patent DNA Extraction
Browse by: Latest US Patents, China's latest patents, Technical Efficacy Thesaurus, Application Domain, Technology Topic, Popular Technical Reports.
© 2024 PatSnap. All rights reserved.Legal|Privacy policy|Modern Slavery Act Transparency Statement|Sitemap|About US| Contact US: help@patsnap.com