Method for catalytic preparation of graphitized particles by cationic resin for treating industrial inorganic wastewater
A cationic resin and inorganic wastewater technology, applied in the direction of inorganic chemistry, chemical instruments and methods, carbon compounds, etc., can solve the problems of high treatment cost, failure to effectively realize the resource utilization of wastewater, etc., and achieve the effect of reducing energy consumption
- Summary
- Abstract
- Description
- Claims
- Application Information
AI Technical Summary
Problems solved by technology
Method used
Image
Examples
Embodiment 1
[0022] A method for preparing graphitized particles by catalyzing a cationic resin for treating industrial inorganic wastewater, comprising the steps of:
[0023] S1. Take a certain amount of nickel-plating wastewater for pretreatment of filtration and concentration, so that there are no particles larger than 100 μm in the nickel-plating wastewater, heat and concentrate the nickel-plating wastewater until the concentration of nickel ions is 1000mg / L, and the cationic resin is 5g according to the feeding ratio / L is put into the nickel-plating wastewater, and the resulting product is placed on a rotary shaker to vibrate for 6 hours at room temperature;
[0024] S2. Filter the product obtained in S1, put the solid in a high-temperature tube furnace through Ar protection (the flow rate is set to 0.2L / min), heat it to 600°C at 5°C / min, and perform high-temperature calcination at 600°C for 1h;
[0025] S3. Take the solid crude product calcined in S2, add hydrochloric acid (1mol / L) ...
Embodiment 2
[0028] A method for preparing graphitized particles by catalyzing a cationic resin for treating industrial inorganic wastewater, comprising the steps of:
[0029] S1. Take a certain amount of nickel-plating wastewater for pretreatment of filtration and concentration, so that there are no particles larger than 100 μm in the nickel-plating wastewater, heat and concentrate the nickel-plating wastewater until the concentration of nickel ions is 500mg / L, and the cationic resin is 10g according to the feeding ratio / L is dropped into the nickel-plating wastewater, and the resulting product is placed on a rotary shaker to vibrate for 12 hours at room temperature;
[0030] S2. Filter the product obtained in S1, and place the solid in a high-temperature tube furnace to pass N 2 Protection (flow rate set to 0.5L / min), heating to 1500°C at 10°C / min, and high-temperature calcination at 1500°C for 3h;
[0031] S3. Take the solid crude product calcined in S2, add hydrochloric acid (1mol / L)...
Embodiment 3
[0034] A method for preparing graphitized particles by catalyzing a cationic resin for treating industrial inorganic wastewater, comprising the steps of:
[0035] S1. Take a certain amount of nickel-plating wastewater for pretreatment of filtration and concentration, so that there are no particles larger than 100 μm in the nickel-plating wastewater, heat and concentrate the nickel-plating wastewater until the concentration of nickel ions is 300mg / L, and the cationic resin is 20g according to the feeding ratio / L is put into the nickel-plating wastewater, and the resulting product is placed on a rotary shaker to vibrate for 48 hours at room temperature;
[0036] S2. Filter the product obtained in S1, and place the solid in a high-temperature tube furnace to pass He and N 2 Mixed gas protection (flow rate set to 2L / min), heated to 1600°C at 20°C / min, and high-temperature calcination at 1600°C for 2h;
[0037] S3. Take the solid crude product after calcining in S2, add hydrochlo...
PUM
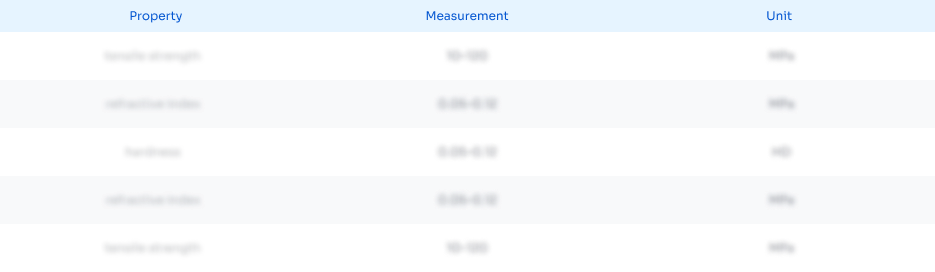
Abstract
Description
Claims
Application Information

- R&D
- Intellectual Property
- Life Sciences
- Materials
- Tech Scout
- Unparalleled Data Quality
- Higher Quality Content
- 60% Fewer Hallucinations
Browse by: Latest US Patents, China's latest patents, Technical Efficacy Thesaurus, Application Domain, Technology Topic, Popular Technical Reports.
© 2025 PatSnap. All rights reserved.Legal|Privacy policy|Modern Slavery Act Transparency Statement|Sitemap|About US| Contact US: help@patsnap.com