Air intake grill hot stamping process and automatic hot stamping line using this process
A technology of air intake grille and assembly line, which is applied in the printing process, printing of special varieties of printed matter, transfer printing, etc. It can solve the problems of poor production flexibility, long production preparation time, and large personnel demand, so as to improve production flexibility. High performance, short production preparation time and good production flexibility
- Summary
- Abstract
- Description
- Claims
- Application Information
AI Technical Summary
Problems solved by technology
Method used
Image
Examples
Embodiment Construction
[0023] The present invention is achieved through the following technical solutions:
[0024] Air intake grill hot stamping process, including the following steps:
[0025] (1) Set the air intake grille on the base;
[0026] (2) Attach a chrome film to the corresponding position of the air intake grille as required;
[0027] (3) According to the hot stamping pattern, place a silicone copy plate on the chrome film that can be used to heat the chrome film to achieve hot stamping and cut off the excess chrome film. The silicone copy plate is provided with an aluminum plate, and the aluminum plate is connected to the heating element Used to heat the silicone copy plate;
[0028] (4) Heat and pressurize the chromium film with a silicone copy plate to realize hot stamping of the chromium film;
[0029] (5) Use the silicone profiling board to cut off the excess chromium film, leaving the hot stamping pattern to complete the hot stamping.
[0030] In the step (2), the chromium film...
PUM
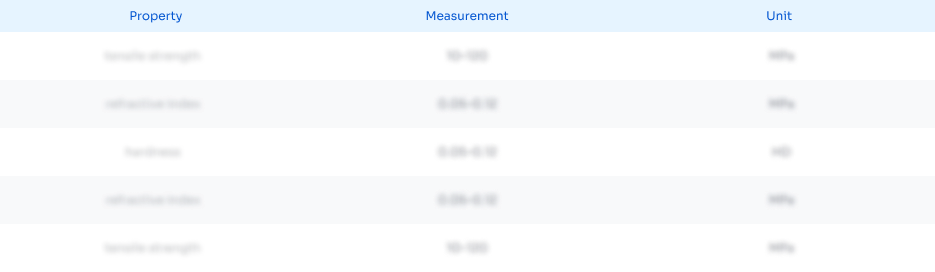
Abstract
Description
Claims
Application Information

- R&D
- Intellectual Property
- Life Sciences
- Materials
- Tech Scout
- Unparalleled Data Quality
- Higher Quality Content
- 60% Fewer Hallucinations
Browse by: Latest US Patents, China's latest patents, Technical Efficacy Thesaurus, Application Domain, Technology Topic, Popular Technical Reports.
© 2025 PatSnap. All rights reserved.Legal|Privacy policy|Modern Slavery Act Transparency Statement|Sitemap|About US| Contact US: help@patsnap.com