Variable speed/variable load rolling bearing fault diagnosis method based on mode conversion
A mode conversion, rolling bearing technology, applied in mechanical bearing testing, character and pattern recognition, testing of mechanical components, etc., can solve problems such as lack of applicable methods, difficulty in diagnosis, unstable vibration signal, etc.
- Summary
- Abstract
- Description
- Claims
- Application Information
AI Technical Summary
Problems solved by technology
Method used
Image
Examples
Embodiment Construction
[0057] Specific embodiments of the present invention such as figure 1 -4 shows a variable speed / variable load rolling bearing fault diagnosis system based on mode conversion, which can realize intelligent diagnosis of bearing faults.
[0058] The rolling bearing fault diagnosis system is used to detect the fault phenomenon of the rolling bearing, and upload the fault vibration signal to the PC. In the specific scheme, the parameter signals are collected by the acceleration sensor on the end cover of the faulty bearing, and these collected parameter signals are processed through the mode conversion technology, so as to distinguish the status of the equipment, and the description of the status of the equipment is the fault phenomenon. Such as bearing inner ring, outer ring, rolling elements and other failure phenomena. The specific calculation method can be calculated by the following formula:
[0059] Outer ring fault formula:
[0060]
[0061] Inner ring fault formula: ...
PUM
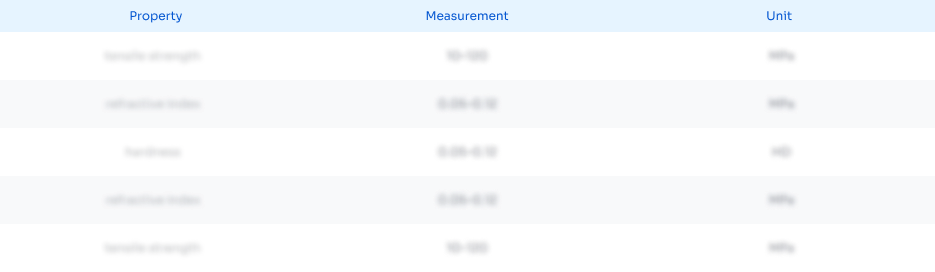
Abstract
Description
Claims
Application Information

- R&D
- Intellectual Property
- Life Sciences
- Materials
- Tech Scout
- Unparalleled Data Quality
- Higher Quality Content
- 60% Fewer Hallucinations
Browse by: Latest US Patents, China's latest patents, Technical Efficacy Thesaurus, Application Domain, Technology Topic, Popular Technical Reports.
© 2025 PatSnap. All rights reserved.Legal|Privacy policy|Modern Slavery Act Transparency Statement|Sitemap|About US| Contact US: help@patsnap.com