Cyanide-free alkaline copper plating solution
A cyanide-free alkaline copper plating and electroplating solution technology, applied in the field of electroplating, can solve problems such as inability to meet demand, too large thickness difference, etc., and achieve the effects of high uniformity and high dispersion ability
- Summary
- Abstract
- Description
- Claims
- Application Information
AI Technical Summary
Problems solved by technology
Method used
Image
Examples
Embodiment 1
[0081] Components and concentrations shown in Table 1 and Table 2 are used to configure the cyanide-free alkaline copper plating electroplating solution, and the concentration of the electroplating solution is 1000ml / L, and then use the electroplating solution to carry out electroplating according to the existing method.
[0082] (1) The preparation method of cyanide-free alkaline copper plating electroplating solution (embodiment 1-embodiment 8):
[0083] Dissolve each complexing agent, copper salt, conductive salt and inorganic base in water according to the components and their concentrations in Table 1 and Table 2, and stir and mix evenly to obtain a cyanide-free alkaline copper plating solution.
[0084] The cyanide-free alkaline copper plating electroplating solution of Comparative Example 1 was prepared according to the components and concentrations thereof in Comparative Example 1.
[0085] Table 1
[0086]
[0087] Table 2
[0088]
[0089]
Embodiment 2
[0101] The aluminum alloy filter can be electroplated according to the following steps by using the existing method.
[0102] (1) Degreasing: 5 minutes at 55°C
[0103] (2) Alkali etching: 50°C for 30 seconds
[0104] (3) Descaling: 90 seconds at 25°C
[0105] (4) Zinc precipitation: 55 seconds at 25°C
[0106] (5) Dezincification: 60 seconds at room temperature
[0107] (6) Zinc precipitation: 25°C for 40 seconds
[0108] (7) Electroplating using the cyanide-free alkaline copper plating solution of Example 4: 1.5A / dm for 40 minutes at 55°C 2
[0109] (8) Burnt copper: 55°C for 20 minutes
[0110] (9) Silver plating: 4 minutes at 28°C
[0111] (10) Silver protection: 45°C for 4-5 minutes
[0112] (11) drying
[0113] (12) Inspection and storage
[0114] All sides of the filter obtained by the above method have a uniform thickness. The thickness difference between the high area and the low area of the workpiece is less than 3 times. After 40 minutes of electroplati...
Embodiment 3
[0116] (1) Thermal shock experiment
[0117] Bake the filter obtained in Example 2 at 220°C, take it out after 60 minutes, put it into cold water immediately, and take it out for observation after 10 minutes. There is no blistering or peeling of the part.
[0118] (2) File experiment
[0119] Utilize a four-inch file to file the edge of the filter obtained in Example 2 along the direction of the metal substrate to the deposition layer and the plating layer at an angle of 45° to remove the deposition layer. It is observed that the deposition layer is not separated from the metal substrate.
[0120] It shows that the above-mentioned electroplating solution not only has a high dispersion ability, but also has a high binding force between the coating and the substrate.
PUM
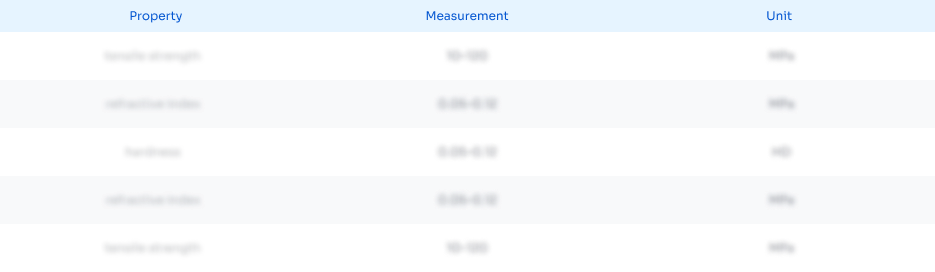
Abstract
Description
Claims
Application Information

- R&D
- Intellectual Property
- Life Sciences
- Materials
- Tech Scout
- Unparalleled Data Quality
- Higher Quality Content
- 60% Fewer Hallucinations
Browse by: Latest US Patents, China's latest patents, Technical Efficacy Thesaurus, Application Domain, Technology Topic, Popular Technical Reports.
© 2025 PatSnap. All rights reserved.Legal|Privacy policy|Modern Slavery Act Transparency Statement|Sitemap|About US| Contact US: help@patsnap.com