Pose measurement and load sensing device for unmanned earth moving machine
A technology of pose measurement and load perception, applied in the direction of earth mover/shovel, construction, etc.
- Summary
- Abstract
- Description
- Claims
- Application Information
AI Technical Summary
Problems solved by technology
Method used
Image
Examples
Embodiment 1
[0021] "A Pose Measurement and Load Sensing Device for Unmanned Operation Process of Earthmoving Machinery with Circular Saw Operating Head".
[0022] attached Figure 4 The utility model is an earth moving machine with a circular saw head. When this type of earthmoving machine is operated by remote control when there is no one on site, it is necessary to accurately adjust the circular saw of the working head to the target point and the appropriate working direction (for example, the working head of the circular saw needs to be perpendicular to the direction of the steel bar or along the existing Grooving direction), at the same time, it is necessary to control the feed speed or feed amount of the working head according to the load change law during the cutting process.
[0023] This embodiment needs to construct the airborne measurement sensing device (refer to the attached figure 1 , which is the core of the present invention) and the remote control end image transmission ...
Embodiment 2
[0031] This embodiment is "a device for pose measurement and load sensing in an unmanned operation process of an earth-moving machine with a hydraulic shearing head". This type of unmanned earthmoving machinery is mainly used for cutting steel bars and other goals in high-risk operations such as building demolition, emergency rescue, explosion protection, rescue and even military industry. It is necessary to accurately adjust the hydraulic shears of the working head to the target point and the appropriate working direction (such as the direction of the vertical steel bar), and at the same time, it is necessary to control the feed speed or feed rate of the hydraulic shears according to the law of load changes during the shearing process. The target pose measurement Especially important with load sensing.
[0032] This embodiment needs to construct the airborne measurement sensing device (refer to the attached figure 1 , which is the core of the present invention) and the remot...
PUM
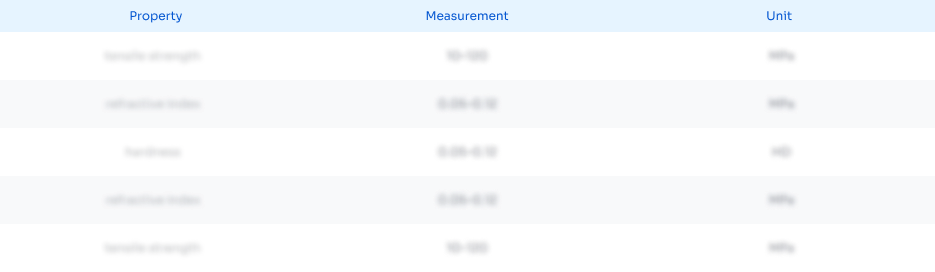
Abstract
Description
Claims
Application Information

- R&D
- Intellectual Property
- Life Sciences
- Materials
- Tech Scout
- Unparalleled Data Quality
- Higher Quality Content
- 60% Fewer Hallucinations
Browse by: Latest US Patents, China's latest patents, Technical Efficacy Thesaurus, Application Domain, Technology Topic, Popular Technical Reports.
© 2025 PatSnap. All rights reserved.Legal|Privacy policy|Modern Slavery Act Transparency Statement|Sitemap|About US| Contact US: help@patsnap.com