Camera calibration system and calibration method thereof
A camera calibration and calibration method technology, applied in the camera calibration system and its calibration field, can solve the problems of misoperation, poor calibration flexibility, time-consuming and inconvenient repeated operation, etc.
- Summary
- Abstract
- Description
- Claims
- Application Information
AI Technical Summary
Problems solved by technology
Method used
Image
Examples
Embodiment 1
[0087] This embodiment provides a camera calibration system, including a calibration platform, the calibration platform includes an X-axis translation mechanism, a Y-axis translation mechanism, a Z-axis translation mechanism; an X-axis rotation mechanism, a Y-axis rotation mechanism, a Z-axis rotation mechanism and Fixed platform; of which:
[0088] The Z-axis translation mechanism is arranged at the bottom of the entire calibration platform, including the base and the Z-axis movement platform, the Z-axis ball screw and the rotary encoder of the Z-axis translation mechanism; the Z-axis ball screw realizes the Z-axis movement of the platform in the Z direction. The movement of the Z-axis translation mechanism is used to record the rotation times of the Z-axis ball screw through the rotary encoder of the Z-axis translation mechanism, thereby recording the position of the Z-axis moving platform in the Z direction;
[0089] The Y-axis translation mechanism includes a Y-axis mobile...
Embodiment 2
[0101] This embodiment provides a calibration method for a camera calibration system, including any one of the following processes:
[0102] - traditional calibration process;
[0103] - Self-calibration process.
[0104] specifically:
[0105] (1) Traditional calibration method
[0106] The specific steps of Zhang Zhengyou's calibration method using the calibration system provided in Example 1 are introduced here:
[0107] The first step: place the calibration platform 10 at a suitable horizontal position, fix the camera 28 at an appropriate position directly above the calibration platform 10; fix the calibration plate 27 on the fixed platform;
[0108] Second step: adjust the X-axis rotation knob 24 of the X-axis rotation bracket, the Y-axis rotation knob 26 of the Y-axis rotation bracket, and the Z-axis rotation knob of the Z-axis rotation bracket 19, so that the X-axis rotation mechanism rotates the encoder 23, Y The rotation angles of the axis rotation mechanism rotar...
PUM
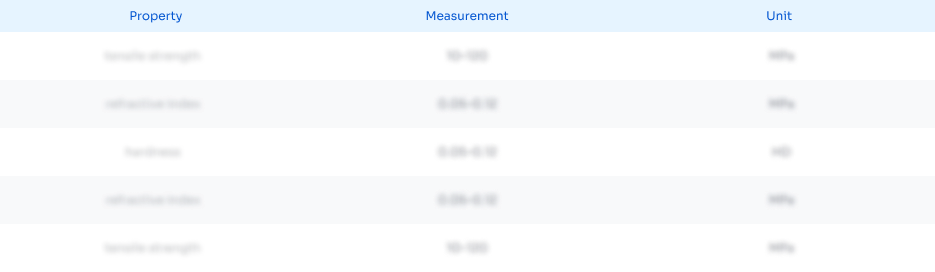
Abstract
Description
Claims
Application Information

- Generate Ideas
- Intellectual Property
- Life Sciences
- Materials
- Tech Scout
- Unparalleled Data Quality
- Higher Quality Content
- 60% Fewer Hallucinations
Browse by: Latest US Patents, China's latest patents, Technical Efficacy Thesaurus, Application Domain, Technology Topic, Popular Technical Reports.
© 2025 PatSnap. All rights reserved.Legal|Privacy policy|Modern Slavery Act Transparency Statement|Sitemap|About US| Contact US: help@patsnap.com