Novel internal structure of reactor and design method and application of novel internal structure
An internal structure and reactor technology, applied in chemical instruments and methods, treatment with moving solid particles, hydrocarbon oil cracking, etc., can solve the problems of easy wear, uneconomical, limited conversion rate of raw materials, etc.
- Summary
- Abstract
- Description
- Claims
- Application Information
AI Technical Summary
Problems solved by technology
Method used
Image
Examples
Embodiment 1
[0023] This embodiment is applied to the oil-coal slurry bed hydrogenation process.
[0024] 1. Feeding process:
[0025] like figure 1 As shown in the figure, after the oil-coal mixture is pressurized by the circulating pump 9, it is sent to the feed port 8 at the bottom of the reactor barrel and enters the inside of the reactor. The flow is then accelerated along the annular gap between the outer wall 5 of the circular frustum cup and the inner wall 3 of the reactor at the bottom of the circulating blister, and finally passes through the annular gap between the outer wall 4 of the cylindrical cup and the inner wall 3 of the reactor. Continue to rise rapidly to the upper section of the circulating bubble cap 1 and enter the reactor, the space suddenly becomes larger, the speed of the mixture suddenly decreases, the light and heavy components are fully separated, the light components flow out from the discharge port 7 at the top, and the heavy components gravity It falls int...
Embodiment 2
[0032] The overall structure is similar to Embodiment 1, which is applied to heavy oil hydrogenation, and also includes 30 hollow blister risers 2 with opening and closing switches. The upper part is close to the bottom surface of the outer wall 4 of the cylindrical cup cover, and the top opening is slightly higher than the upper periphery of the cylindrical cup cover, such as figure 2 , 3 As shown, the inner diameter of the blister riser 2 is 10 mm.
[0033] The material can also rise rapidly to the top of the circulating blister through the blister riser 2, and its rising speed is close to the annular gap between the outer wall 4 of the cylindrical cup and the inner wall 3 of the reactor, and the number of opening and closing of the blister riser 2 is controlled according to the situation. , so that the rising speed of the material can be better controlled.
[0034] in conclusion:
[0035] It can be seen from the above examples that the hydrogenation reactor of the prese...
PUM
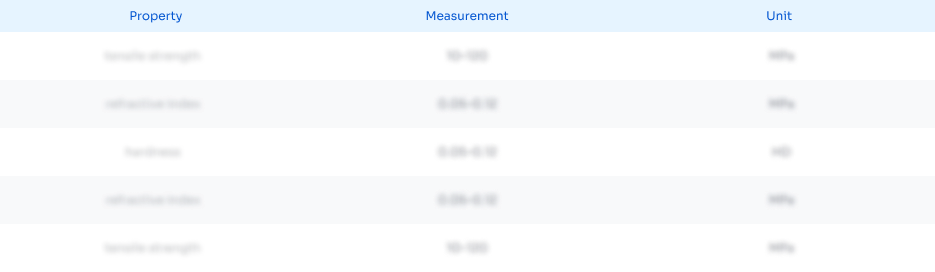
Abstract
Description
Claims
Application Information

- R&D Engineer
- R&D Manager
- IP Professional
- Industry Leading Data Capabilities
- Powerful AI technology
- Patent DNA Extraction
Browse by: Latest US Patents, China's latest patents, Technical Efficacy Thesaurus, Application Domain, Technology Topic, Popular Technical Reports.
© 2024 PatSnap. All rights reserved.Legal|Privacy policy|Modern Slavery Act Transparency Statement|Sitemap|About US| Contact US: help@patsnap.com