Powder metallurgy method
A technology of powder metallurgy and tungsten powder, which is applied in metal processing equipment, transportation and packaging, etc., can solve the problem of low strength and achieve the effect of improving tensile strength and hardness
- Summary
- Abstract
- Description
- Claims
- Application Information
AI Technical Summary
Problems solved by technology
Method used
Examples
Embodiment Construction
[0011] Below in conjunction with the examples, the specific implementation of the present invention will be further described in detail. The following examples are used to illustrate the present invention, but are not intended to limit the scope of the present invention.
[0012] A powder metallurgy method of the present invention contains 6.8% of micropowder wax, 1.1-3.2% of polyethylene powder, 1.1-2.2% of zinc stearate, 4.3% of anti-wear agent, 5% of tungsten powder and the rest is aluminum powder by weight and impurities that are difficult to remove; the above powder is stirred with a mixer at a high temperature of 260-280°C for 5-6 hours, fully mixed, and then die-casted and deburred to obtain a finished product.
[0013] The zinc stearate weight ratio is 2%. The weight ratio of the polyethylene powder is 3%.
[0014] The powder metallurgy method of the invention greatly improves the tensile strength and hardness of the product.
PUM
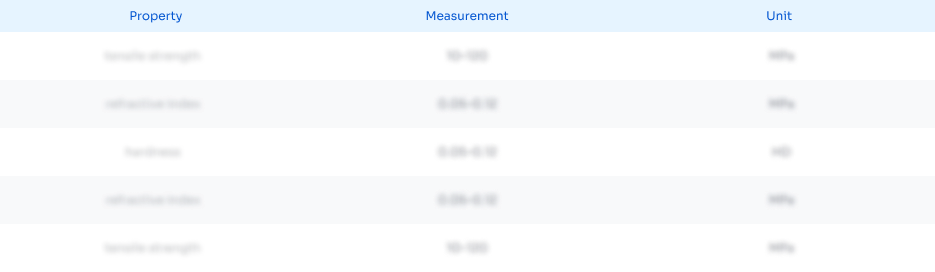
Abstract
Description
Claims
Application Information

- R&D
- Intellectual Property
- Life Sciences
- Materials
- Tech Scout
- Unparalleled Data Quality
- Higher Quality Content
- 60% Fewer Hallucinations
Browse by: Latest US Patents, China's latest patents, Technical Efficacy Thesaurus, Application Domain, Technology Topic, Popular Technical Reports.
© 2025 PatSnap. All rights reserved.Legal|Privacy policy|Modern Slavery Act Transparency Statement|Sitemap|About US| Contact US: help@patsnap.com