High-strength high-thermal conductivity copper alloy and preparation method thereof
A copper alloy, high thermal conductivity technology, applied in the field of alloy materials, can solve problems such as high price, increased material cost, and physical hazards, achieve good thermal conductivity and thermal fatigue resistance, increase casting and rolling speed, and reduce thermal resistance.
- Summary
- Abstract
- Description
- Claims
- Application Information
AI Technical Summary
Problems solved by technology
Method used
Image
Examples
Embodiment 1
[0018] The copper alloy prepared in this embodiment is composed of the following components in terms of mass percentage: Ni: 3.5%; Co: 2.5%; Si: 1.0%; Be: 0.5%, and the balance is Cu and unavoidable impurities. The copper alloy method that present embodiment prepares is as follows:
[0019] (1) Melting, according to the mass ratio of the above components, place the simple substances of each component in a vacuum induction melting furnace for melting, and melt at a temperature of 1250° C. for 40 to 60 minutes.
[0020] (2) Casting: Pour the smelted molten metal into the rotating mold, fill the mold under the action of centrifugal force and solidify and form, the rotation speed is: stepless speed change 100-300r / min.
[0021] (3) Forging, the billet is hot forged, then cooled to room temperature, the initial forging temperature is 900°C, and the final forging temperature is 800°C.
[0022] (4) Heat treatment, heat treatment includes solid solution + aging, heat the forging afte...
Embodiment 2
[0025] The copper alloy prepared in this embodiment is composed of the following components in terms of mass percentage: Ni: 3.6%; Co: 2.4%; Si: 1.2%; Be: 0.6%, and the balance is Cu and unavoidable impurities. The method for preparing the copper alloy in this embodiment is the same as that in Example 1, wherein the solution treatment temperature is 870°C, the degree of primary aging treatment is 260°C, and the degree of secondary aging treatment is 460°C. The performance parameters of the copper alloy material prepared in this embodiment are shown in Table 1.
Embodiment 3
[0027] The copper alloy prepared in this embodiment is composed of the following components in terms of mass percentage: Ni: 3.7%; Co: 2.3%; Si: 1.4%; Be: 0.7%, and the balance is Cu and unavoidable impurities. The copper alloy prepared in this embodiment is the same as in Example 1, wherein the solution treatment temperature is 880°C, the degree of primary aging treatment is 270°C, and the degree of secondary aging treatment is 470°C. The performance parameters of the copper alloy material prepared in this embodiment are shown in Table 1.
PUM
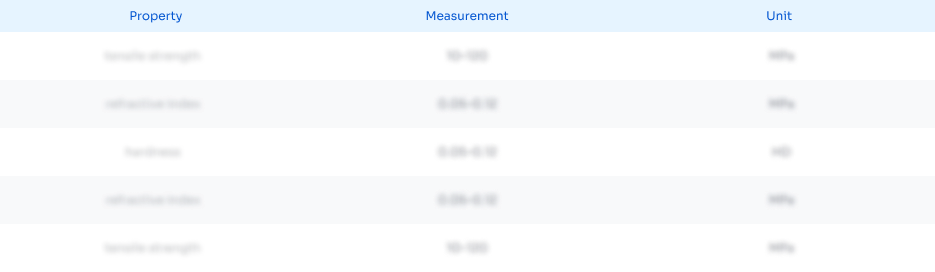
Abstract
Description
Claims
Application Information

- R&D
- Intellectual Property
- Life Sciences
- Materials
- Tech Scout
- Unparalleled Data Quality
- Higher Quality Content
- 60% Fewer Hallucinations
Browse by: Latest US Patents, China's latest patents, Technical Efficacy Thesaurus, Application Domain, Technology Topic, Popular Technical Reports.
© 2025 PatSnap. All rights reserved.Legal|Privacy policy|Modern Slavery Act Transparency Statement|Sitemap|About US| Contact US: help@patsnap.com