Flexible adhesive of polyethylene polypropylene waterproof coiled material and preparation method of flexible adhesive
A polyethylene polypropylene fiber and waterproof membrane technology, which is applied in the directions of adhesives, polymer adhesive additives, non-polymer adhesive additives, etc. Engineering failure, easy cracking of the adhesive, etc
- Summary
- Abstract
- Description
- Claims
- Application Information
AI Technical Summary
Problems solved by technology
Method used
Image
Examples
Embodiment 1
[0045] Measure 30 parts of cement, 15 parts of heavy calcium, 40 parts of quartz powder, 6 parts of water-retaining agent, and 9 parts of thickener, respectively, and then add them to the mixing tank for mixing and stirring. , and then 50 parts of 400 emulsion, 35 parts of 707 emulsion, 13 parts of water, and 2 parts of defoamer were measured respectively, and then added to the mixing tank with blades for stirring. The stirring time was 30-40min. After stirring for 20-30min Add defoamer. After fully stirring, a liquid material is obtained. At the construction site, the liquid material and the powder material are stirred evenly at a ratio of 1:3 to obtain a flexible adhesive for polyethylene polypropylene fiber waterproofing membrane.
Embodiment 2
[0047] Measure 35 parts of cement, 10 parts of heavy calcium, 38 parts of quartz powder, 7 parts of water-retaining agent, and 10 parts of thickener, respectively, and add them into the mixing tank for mixing and stirring. , and then 55 parts of 400 emulsion, 30 parts of 707 emulsion, 14 parts of water, and 1 part of defoamer were measured respectively, and then added to the stirring tank with blades for stirring. The stirring time was 30-40min. After stirring for 20-30min Add defoamer. After fully stirring, a liquid material is obtained. At the construction site, the liquid material and the powder material are stirred evenly at a ratio of 1:3 to obtain a flexible adhesive for polyethylene polypropylene fiber waterproofing membrane.
Embodiment 3
[0049] Measure 40 parts of cement, 20 parts of heavy calcium, 30 parts of quartz powder, 4 parts of water-retaining agent, and 6 parts of thickener, respectively, and add them into the mixing tank for mixing and stirring. , and then 55 parts of 400 emulsion, 30 parts of 707 emulsion, 14 parts of water, and 1 part of defoamer were measured respectively, and 14 parts of 400 emulsion, 707 emulsion and water were added to the stirring tank with paddle blades for stirring. The stirring time 30-40min, add defoamer after stirring for 20-30min. After fully stirring, a liquid material is obtained. At the construction site, the liquid material and the powder material are stirred evenly at a ratio of 1:3 to obtain a flexible adhesive for polyethylene polypropylene fiber waterproofing membrane.
PUM
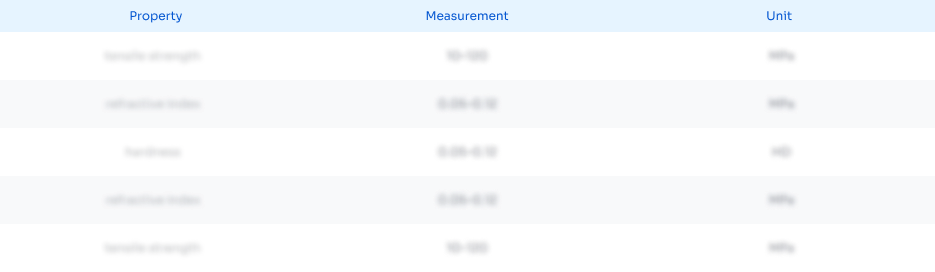
Abstract
Description
Claims
Application Information

- Generate Ideas
- Intellectual Property
- Life Sciences
- Materials
- Tech Scout
- Unparalleled Data Quality
- Higher Quality Content
- 60% Fewer Hallucinations
Browse by: Latest US Patents, China's latest patents, Technical Efficacy Thesaurus, Application Domain, Technology Topic, Popular Technical Reports.
© 2025 PatSnap. All rights reserved.Legal|Privacy policy|Modern Slavery Act Transparency Statement|Sitemap|About US| Contact US: help@patsnap.com