Design method for reducing assembly stress of main shaft and impeller and bending deformation of main shaft
A technology of bending deformation and spindle, which is applied in the fields of manufacturing and assembly, and large-scale mechanical equipment design. It can solve problems such as stress concentration and bending deformation of the spindle, and achieve the effects of reducing the degree of bending deformation, simplifying the manufacturing process, and reducing contact pressure.
- Summary
- Abstract
- Description
- Claims
- Application Information
AI Technical Summary
Problems solved by technology
Method used
Image
Examples
Embodiment 1
[0033] Embodiment 1 Analysis of influence of semicircular groove structure on assembly performance
[0034] A. Set the corresponding thermal boundary conditions and mechanical boundary conditions according to the actual assembly conditions.
[0035] B. Calculate the main shaft bending deformation, Mises stress, contact pressure and friction torque when the groove is not set as a comparative example, and record it in Table 2.
[0036] C. On the original model, set the end face of the bottom 3 side close to the main shaft 5 as follows Figure 4 and Figure 5 For the circular groove with a semicircular section shown, the radius of the circle and the position of the center of the circle are used as design parameters.
[0037] D. Calculate the corresponding spindle bending deformation, Mises stress, contact pressure and friction torque at different radii and different center positions as shown in Table 2.
[0038] E. Make a comprehensive comparison of the data in Table 2 (the mo...
PUM
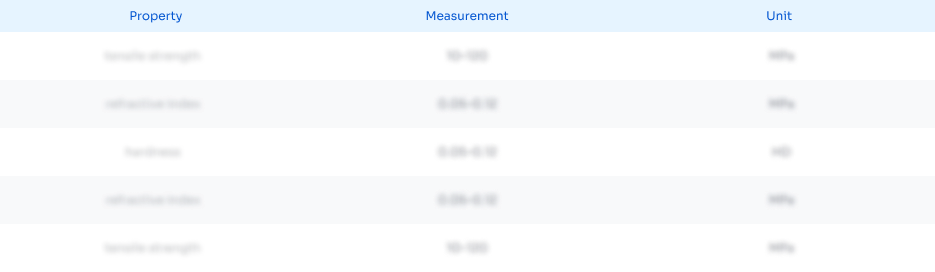
Abstract
Description
Claims
Application Information

- R&D
- Intellectual Property
- Life Sciences
- Materials
- Tech Scout
- Unparalleled Data Quality
- Higher Quality Content
- 60% Fewer Hallucinations
Browse by: Latest US Patents, China's latest patents, Technical Efficacy Thesaurus, Application Domain, Technology Topic, Popular Technical Reports.
© 2025 PatSnap. All rights reserved.Legal|Privacy policy|Modern Slavery Act Transparency Statement|Sitemap|About US| Contact US: help@patsnap.com