Automatic brazing process for heating disc production
A technology of brazing process and heating plate, which is applied in metal processing, manufacturing tools, welding equipment, etc., can solve the problems of difficulty in guaranteeing welding quality, difficulty in getting the best of both worlds, high proportion of slag inclusion and air holes, etc., to improve brazing quality and brazing Welding efficiency, reduction of labor factors, and the effect of reducing manufacturing costs
- Summary
- Abstract
- Description
- Claims
- Application Information
AI Technical Summary
Problems solved by technology
Method used
Image
Examples
Embodiment 1
[0039] The automatic brazing process for the production of heating discs according to the present invention, the brazing process described in this embodiment includes the following steps:
[0040] (1) Coating of aluminum flux: prepare aluminum flux slurry with water, wherein the weight ratio of aluminum flux to water is: flux: water = 1:2, and the method of quantitatively dipping with a brush , brushed onto the surface of heat-conducting aluminum plates and stainless steel discs; due to the single and fixed operation, it can be designed as an automated mechanical action;
[0041] (2) Aluminum solder paste coating: use a pressure dispenser to quantitatively inject aluminum solder paste into the position to be brazed on the thermally conductive aluminum plate by controlling the dispensing pressure, dispensing time, and moving track of the dispenser. Due to the single operation and Fixed, can be designed as automatic mechanical action; wherein, the amount of aluminum solder paste...
Embodiment 2
[0048] The automatic brazing process for the production of heating discs according to the present invention, the brazing process described in this embodiment includes the following steps:
[0049] (1) Coating of aluminum flux: prepare aluminum flux slurry with water, wherein the weight ratio of aluminum flux to water is: flux: water = 1:5, and the method of quantitatively dipping with a brush , brushed onto the surface of heat-conducting aluminum plates and stainless steel discs; due to the single and fixed operation, it can be designed as an automated mechanical action;
[0050] (2) Coating of aluminum solder paste: A pressure-type dispensing machine is used to quantitatively inject aluminum solder paste to the position to be brazed on the thermal conductor aluminum plate by controlling the dispensing pressure, dispensing time, and moving track of the dispensing machine. Due to the single operation And fixed, it can be designed as an automatic mechanical action; wherein, the ...
Embodiment 3
[0057] The automatic brazing process for the production of heating discs according to the present invention, the brazing process described in this embodiment includes the following steps:
[0058] (1) Coating of aluminum flux: Prepare aluminum flux slurry with water, wherein the weight ratio of aluminum flux to water is: flux: water = 1:3, and the method of quantitatively dipping with a brush , brushed onto the surface of heat-conducting aluminum plates and stainless steel discs; due to the single and fixed operation, it can be designed as an automated mechanical action;
[0059] (2) Aluminum solder paste coating: use a pressure dispenser to quantitatively inject aluminum solder paste into the position to be brazed on the thermally conductive aluminum plate by controlling the dispensing pressure, dispensing time, and moving track of the dispenser. Due to the single operation and Fixed, can be designed as automatic mechanical action; wherein, the amount of aluminum solder paste...
PUM
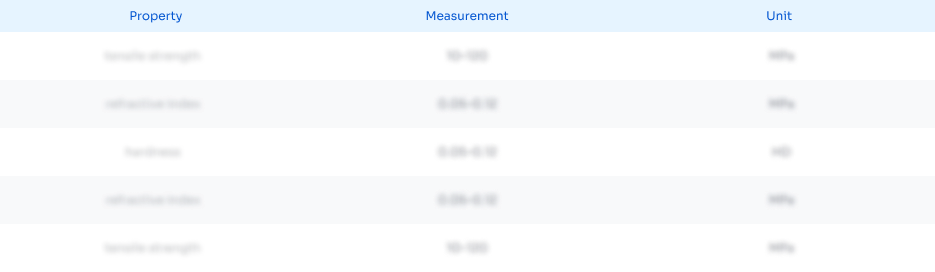
Abstract
Description
Claims
Application Information

- R&D Engineer
- R&D Manager
- IP Professional
- Industry Leading Data Capabilities
- Powerful AI technology
- Patent DNA Extraction
Browse by: Latest US Patents, China's latest patents, Technical Efficacy Thesaurus, Application Domain, Technology Topic, Popular Technical Reports.
© 2024 PatSnap. All rights reserved.Legal|Privacy policy|Modern Slavery Act Transparency Statement|Sitemap|About US| Contact US: help@patsnap.com