Implementation method applied to flexible line higher pair constraint simplification model
A technology that simplifies models and implementation methods, applied in the field of simulation, can solve the problems of many burrs in simulation results, poor calculation stability, low calculation efficiency, etc., and achieve the effects of smooth simulation results without burrs, reliable efficiency, and good stability
- Summary
- Abstract
- Description
- Claims
- Application Information
AI Technical Summary
Problems solved by technology
Method used
Image
Examples
Embodiment Construction
[0034] The present invention will be described in detail below with reference to the accompanying drawings and embodiments.
[0035] The present invention provides an implementation method applied to a simplified model of high pair constraints of flexible lines. The technical solutions and application examples of the present invention are described in detail with reference to the accompanying drawings.
[0036] Taking the key parts in the vector nozzle mechanism as an example for analysis, the flexible member A in the present invention is the converging skeleton of the embodiment, and the roller is the A8 roller of the embodiment.
[0037] Considering that there is still a soft body contact between the ring and the convergent skeleton in the simplified model, and this group of contacts has more elements after the A8 ring has been flexed and the surface of the outer contour element is large, the calculation amount of the contact detection search is also relatively large. And it...
PUM
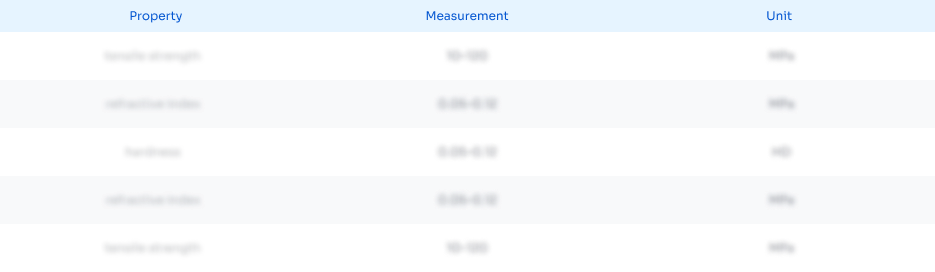
Abstract
Description
Claims
Application Information

- R&D Engineer
- R&D Manager
- IP Professional
- Industry Leading Data Capabilities
- Powerful AI technology
- Patent DNA Extraction
Browse by: Latest US Patents, China's latest patents, Technical Efficacy Thesaurus, Application Domain, Technology Topic, Popular Technical Reports.
© 2024 PatSnap. All rights reserved.Legal|Privacy policy|Modern Slavery Act Transparency Statement|Sitemap|About US| Contact US: help@patsnap.com