Preparation and application of amorphous nanocrystalline alloy
An amorphous nanocrystalline and alloy technology, applied in water/sludge/sewage treatment, water pollutants, water/sewage treatment, etc., can solve the problems of low degradation efficiency, low cost, easy oxidation, etc. Forming ability, low cost, the effect of accelerated decomposition
- Summary
- Abstract
- Description
- Claims
- Application Information
AI Technical Summary
Problems solved by technology
Method used
Examples
Embodiment 1
[0024] A kind of preparation of amorphous nanocrystalline alloy specifically comprises the following steps:
[0025] (1) Weigh each raw material according to the content of each element in the alloy; the content of each element is calculated by mass percentage, including Ni0.5%, Co 0.3%, Cu 2%, Nb 0.01%, B 3%, Si 2%, C 3.5%, P 0.1%, the balance is Fe, and the sum of the contents of each component is 100%;
[0026] (2) Place the above-mentioned weighed raw materials in a vacuum induction furnace for stirring and melting to obtain a master alloy ingot; wherein, the conditions for the melting are: the degree of vacuum is 0.004Pa, the temperature is 1250°C, the stirring speed is 500rpm, and the smelting The time is 3 minutes, and the number of smelting is 5 times;
[0027] (3) Grinding the surface of the master alloy ingot obtained in step (2) to remove scale, then crushing, and then preparing strips by a single-roller spin quenching method; wherein, the copper roller speed of th...
Embodiment 2
[0031] A kind of preparation of amorphous nanocrystalline alloy specifically comprises the following steps:
[0032] (1) Weigh each raw material according to the content of each element in the alloy; the content of each element is calculated by mass percentage, including Ni8%, Co 0.3%, Cu 1%, Nb 0.03%, B 11%, Si 9%, C 0.01% , P 0.1%, the balance is Fe, and the sum of the contents of each component is 100%;
[0033] (2) Place the above-mentioned weighed raw materials in a vacuum induction furnace for stirring and melting to obtain a master alloy ingot; wherein, the conditions for the melting are: a vacuum degree of 0.004Pa, a temperature of 1450°C, a stirring speed of 500rpm, and smelting The time is 3 minutes, and the number of smelting is 5 times;
[0034] (3) Grinding the surface of the master alloy ingot obtained in step (2) to remove scale, then crushing, and then preparing strips by a single-roller spin quenching method; wherein, the copper roller speed of the single-rol...
Embodiment 3
[0038] A kind of preparation of amorphous nanocrystalline alloy specifically comprises the following steps:
[0039] (1) Weigh each raw material according to the content of each element in the alloy; the content of each element is calculated by mass percentage, including Ni2%, Co 0.15%, Cu 1.2%, Nb 0.015%, B 5%, Si 4%, C 1% , P 3%, the balance is Fe, and the sum of the contents of each component is 100%;
[0040] (2) Place the above-mentioned weighed raw materials in a vacuum induction furnace and stir and smelt to obtain a master alloy ingot; wherein, the conditions for the smelting are: a vacuum degree of 0.004Pa, a temperature of 1300°C, a stirring speed of 500rpm, and smelting The time is 3 minutes, and the number of smelting is 5 times;
[0041] (3) Grinding the surface of the master alloy ingot prepared in step (2) to remove scale, then crushing, and then preparing strips by a single-roller spin quenching method; wherein, the copper roller speed of the single-roller spi...
PUM
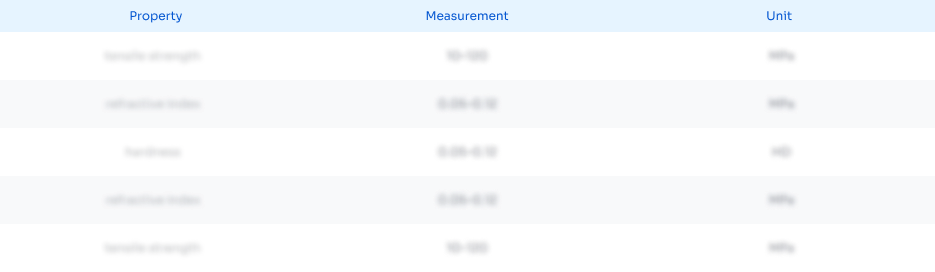
Abstract
Description
Claims
Application Information

- R&D
- Intellectual Property
- Life Sciences
- Materials
- Tech Scout
- Unparalleled Data Quality
- Higher Quality Content
- 60% Fewer Hallucinations
Browse by: Latest US Patents, China's latest patents, Technical Efficacy Thesaurus, Application Domain, Technology Topic, Popular Technical Reports.
© 2025 PatSnap. All rights reserved.Legal|Privacy policy|Modern Slavery Act Transparency Statement|Sitemap|About US| Contact US: help@patsnap.com