Dynamic detection system and method for geometric parameters of vehicle-mounted non-contact overhead line system
A geometric parameter and dynamic detection technology, applied in the field of detection, can solve the problems of complex structure, difficult installation, low precision, etc., and achieve the effect of high detection precision, simple structure and wide versatility
- Summary
- Abstract
- Description
- Claims
- Application Information
AI Technical Summary
Problems solved by technology
Method used
Image
Examples
Embodiment 1
[0035] This embodiment provides a vehicle-mounted non-contact type catenary geometric parameter dynamic detection system. Such as figure 1 As shown, it includes a geometric detection unit located on the top of the vehicle body for detecting the contact net, a control unit provided inside the vehicle body, and a vibration compensation unit located on the bottom of the vehicle body for detecting vibration of the vehicle body.
[0036] The vibration compensation unit is located at the bottom of the vehicle and is composed of two two-dimensional contour scanning sensors; and the geometric detection unit and the vibration compensation unit are installed in the same cross section of the vehicle body perpendicular to the rail.
[0037] Such as figure 2 , image 3 As shown, the geometric detection unit is located in the center of the car body and includes a lidar and four line array cameras, a light source and a mounting bracket. The lidar and line scan cameras are installed on the top of ...
Embodiment 2
[0042] This embodiment provides a detection method to which Embodiment 1 is applied.
[0043] It includes the following steps:
[0044] S1. Use lidar and line array camera to detect the spatial position of the catenary on the roof of the vehicle.
[0045] Before the actual inspection, calibrate the line scan camera, the process is as follows.
[0046] S11. Use regression technology to calibrate the line scan camera used to measure the catenary in advance.
[0047] S111 Obtain training data, and obtain the correspondence between world coordinates and pixel coordinates of the line array camera;
[0048] In the calibration process, usually an object with known spatial position information is used as a scene for shooting, such an object is called a calibration object. In this embodiment, a black strip is used as a calibration object, and the shooting is performed from several visions. Considering that the target surface of the line scan camera is relatively large, and in order to make the ...
PUM
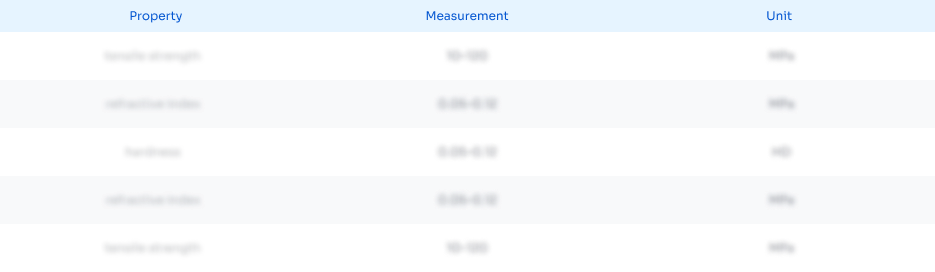
Abstract
Description
Claims
Application Information

- R&D
- Intellectual Property
- Life Sciences
- Materials
- Tech Scout
- Unparalleled Data Quality
- Higher Quality Content
- 60% Fewer Hallucinations
Browse by: Latest US Patents, China's latest patents, Technical Efficacy Thesaurus, Application Domain, Technology Topic, Popular Technical Reports.
© 2025 PatSnap. All rights reserved.Legal|Privacy policy|Modern Slavery Act Transparency Statement|Sitemap|About US| Contact US: help@patsnap.com