Polyethylene masterbatch and preparation method thereof
A technology of polyethylene and color masterbatch, applied in the field of polyethylene color masterbatch and its preparation, can solve the problems of time-consuming, hopper manpower and other problems, and achieve the effects of broad application prospects, strong tinting strength and good dispersion performance.
- Summary
- Abstract
- Description
- Claims
- Application Information
AI Technical Summary
Problems solved by technology
Method used
Examples
Embodiment 1
[0027] A polyethylene color masterbatch is made of the following raw materials in parts by weight: 62 parts of thermoplastic polyethylene resin powder, 4.2 parts of EVA resin, 3.6 parts of heavy calcium carbonate, 1.8 parts of polyethylene wax, and 30 parts of pigment.
[0028] The preparation method of described polyethylene color masterbatch, the steps are as follows:
[0029] (1) Mixing by high-speed internal mixer: first add powdery polyethylene resin and polyethylene wax, premix at high speed, the screw speed is 425RPM, the temperature is set at 25°C, and the time is 750 seconds; then add heavy High-quality calcium carbonate and pigments, high-speed premixing, the screw speed is 365RPM, the temperature is set to 26°C, the time is 720 seconds, and finally EVA resin is added, the screw speed is 370RPM, the temperature is set to 26°C, and the time is 450 seconds, obtain mixed base material;
[0030] (2) Mixing: the base material is extruded to obtain a polyethylene profile,...
Embodiment 2
[0035] A polyethylene color masterbatch is made of the following raw materials in parts by weight: 68 parts of thermoplastic polyethylene resin powder, 4.5 parts of EVA resin, 4.3 parts of heavy calcium carbonate, 1.2 parts of polyethylene wax, and 32 parts of pigment.
[0036] The preparation method of described polyethylene color masterbatch, the steps are as follows:
[0037] (1) Mixing by high-speed internal mixer: first add powdery polyethylene resin and polyethylene wax, premix at high speed, the screw speed is 430RPM, the temperature is set at 22°C, and the time is 800 seconds; then add heavy High-quality calcium carbonate and pigment, high-speed premixing, the screw speed is 380RPM, the temperature is set to 28 ° C, the time is 600 seconds, and finally EVA resin is added, the screw speed is 380 RPM, the temperature is set to 25 ° C, the time is 510 seconds, obtain mixed base material;
[0038] (2) Mixing: the base material is extruded to obtain a polyethylene profile,...
Embodiment 3
[0043] A polyethylene color masterbatch is made of the following raw materials in parts by weight: 50 parts of thermoplastic polyethylene resin powder, 3.4 parts of EVA resin, 2.8 parts of heavy calcium carbonate, 2.5 parts of polyethylene wax, and 28 parts of pigment.
[0044] The preparation method of described polyethylene color masterbatch, the steps are as follows:
[0045] (1) Mixing by high-speed internal mixer: first add powdered polyethylene resin and polyethylene wax, premix at high speed, the screw speed is 420RPM, the temperature is set at 28°C, and the time is 720 seconds; then add heavy High-quality calcium carbonate and pigments are premixed at high speed. The screw speed is 360RPM, the temperature is set at 25°C, and the time is 750 seconds. Finally, EVA resin is added. The screw speed is 360RPM, the temperature is set at 28°C, and the time is 420 seconds, obtain mixed base material;
[0046] (2) Mixing: Extrude the base material to obtain a polyethylene profi...
PUM
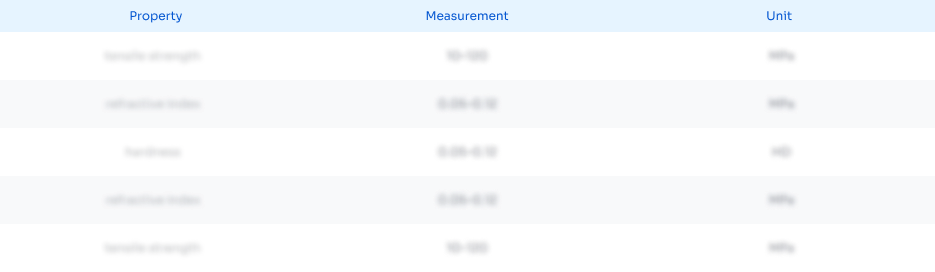
Abstract
Description
Claims
Application Information

- R&D Engineer
- R&D Manager
- IP Professional
- Industry Leading Data Capabilities
- Powerful AI technology
- Patent DNA Extraction
Browse by: Latest US Patents, China's latest patents, Technical Efficacy Thesaurus, Application Domain, Technology Topic, Popular Technical Reports.
© 2024 PatSnap. All rights reserved.Legal|Privacy policy|Modern Slavery Act Transparency Statement|Sitemap|About US| Contact US: help@patsnap.com