Self-thermal-insulation wall and manufacturing technology thereof
A self-insulation, wall technology, applied in covering/lining, construction, building structure, etc., can solve the problem that the bonding between foam concrete and cement pressure plate is not strong enough, the insulation effect of foam concrete is not ideal, and the service life of the wall is reduced, etc. problems, to achieve the effect of facilitating mechanized production, less mold support and mold removal processes, and saving templates
- Summary
- Abstract
- Description
- Claims
- Application Information
AI Technical Summary
Problems solved by technology
Method used
Image
Examples
Embodiment Construction
[0044] Embodiments of the technical solutions of the present invention will be described in detail below in conjunction with the accompanying drawings. The following examples are only used to illustrate the technical solutions of the present invention more clearly, and therefore are only examples, rather than limiting the protection scope of the present invention.
[0045] Such as Figure 1-Figure 7 The shown self-insulation wall includes a main body frame 1, a main keel 2, an outer insulation layer 3, an insulation core layer and an inner insulation layer 5; the outer insulation layer 3 and the inner insulation layer 5 are respectively arranged on both sides of the insulation core layer; The inner and outer insulation layers are prefabricated into blocks and then assembled.
[0046] The main frame 1 of this embodiment is a concrete frame, including vertically arranged structural columns 11 and horizontally arranged structural beams 12 between the structural columns 11; betwe...
PUM
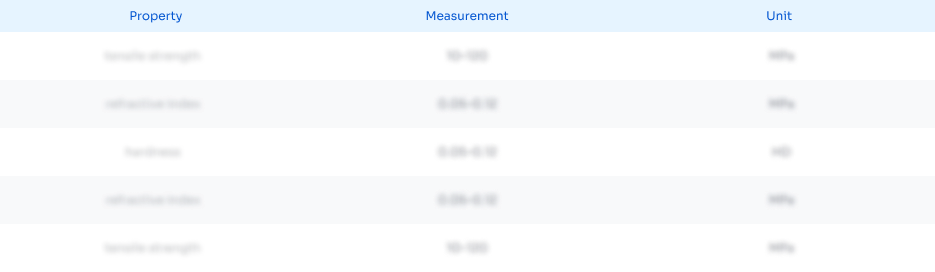
Abstract
Description
Claims
Application Information

- R&D
- Intellectual Property
- Life Sciences
- Materials
- Tech Scout
- Unparalleled Data Quality
- Higher Quality Content
- 60% Fewer Hallucinations
Browse by: Latest US Patents, China's latest patents, Technical Efficacy Thesaurus, Application Domain, Technology Topic, Popular Technical Reports.
© 2025 PatSnap. All rights reserved.Legal|Privacy policy|Modern Slavery Act Transparency Statement|Sitemap|About US| Contact US: help@patsnap.com