Preparation method of polyurethane hot melt adhesive adhered with lower surface energy material
A polyurethane hot-melt adhesive, low surface energy technology, used in polyurea/polyurethane adhesives, adhesives, adhesive types, etc., can solve the problems of poor bonding performance of low surface energy materials, and overcome the difference in expansion coefficient. , the effect of excellent low surface energy bonding properties, good flexibility and bulk tensile strength
- Summary
- Abstract
- Description
- Claims
- Application Information
AI Technical Summary
Problems solved by technology
Method used
Image
Examples
Embodiment 1
[0027] 1) Add 20 parts of hydroxyl-terminated polybutadiene liquid rubber (HTPB), 15 parts of polyether polyol PPG210, and 4 parts of adhesion promoter 2,2 dimethylol butyric acid into the reaction kettle, at 110 ° C, Dehydration at -0.095MPa for 2 hours, lower the temperature to 80°C, add 0.05 part of dibutyltin dilaurate, 22 parts of toluene diisocyanate TDI80, stir at 700 rpm, and react at 80°C for 1 hour. Then add 15 parts of reactive end-capping coupling agent mercaptopropyltriethoxysilane (KH-580) and react at 70° C. for 2 hours to obtain a prepolymer end-capped by the coupling agent.
[0028] 2) Dehydrate 60 parts of polyester polyol CMA-66 and 15 parts of polyether polyol PTMG3000 at 120°C and -0.095MPa for 2 hours. After dehydration, add 4,4' diphenylmethane diisocyanate MDI 35 parts, stirred at a speed of 700 rpm, reacted at 110°C for 3 hours, then added 10 parts of the coupling agent-capped prepolymer prepared in step 1 and 0.1 part of dimorpholino diethyl ether, R...
Embodiment 2
[0030]1) Add 5 parts of polybutadiene polyether glycol, 40 parts of polyether polyol PTMG2000, and 8 parts of 4-hydroxybutyric acid into the reaction kettle, dehydrate at 110°C and -0.095MPa for 2 hours, and cool down to 80°C , add 0.01 part of stannous octoate, 10 parts of polyisocyanate Desmodur N3300, stir at a speed of 400 rpm, react at 65 ° C for 3 hours, then add reaction-blocking coupling agent mercaptopropyltrimethoxysilane ( 2 parts of KH-590) were reacted at 90°C for 5 hours to obtain a prepolymer capped by a coupling agent.
[0031] 2) Dehydrate 35 parts of polyester polyol CMA-44 and 40 parts of polyether polyol PPG220 at 120°C and -0.095MPa for 2 hours. Stir at a speed of 1 / min, react at 120°C for 1 hour, then add 35 parts of the coupling agent-capped prepolymer prepared in step 1 and 0.001 part of triethylenediamine, raise the temperature to 110°C, and evacuate to - Below 0.095MPa, remove the air bubbles for 30 minutes, discharge the material, and seal the packa...
Embodiment 3
[0033] 1) Add 13 parts of hydroxyl-terminated butadiene acrylonitrile liquid rubber (HTBN), 28 parts of polyether polyol PTMG3000, and 1 part of dodecenyl succinic acid into the reaction kettle. Dehydrate for 2 hours, lower the temperature to 80°C, add 0.03 parts of triethylenediamine, 40 parts of toluene diisocyanate TDI 100, stir at 550 rpm, react at 85°C for 2 hours, then add reaction-capped coupling Add 8 parts of ethylenediaminopropyltrimethoxysilane (KH-792) to react at 80°C for 3 hours to prepare a prepolymer capped by a coupling agent.
[0034] 2) Dehydrate 47 parts of polyester polyol CMA-66 and 27 parts of polyether polyol PPG220 at 120°C and -0.095MPa for 2 hours. After dehydration is completed, add 24 parts of Desmodur N3300. Stir at a rotating speed, react at 100°C for 3 hours, then add 23 parts of the coupling agent-capped prepolymer prepared in step 1, 0.05 part of stannous octoate, heat up to 110°C, evacuate to below -0.095MPa, remove Bubbling for 30 minutes, ...
PUM
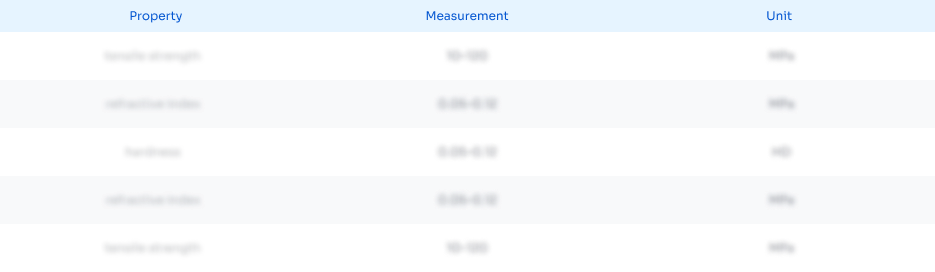
Abstract
Description
Claims
Application Information

- R&D
- Intellectual Property
- Life Sciences
- Materials
- Tech Scout
- Unparalleled Data Quality
- Higher Quality Content
- 60% Fewer Hallucinations
Browse by: Latest US Patents, China's latest patents, Technical Efficacy Thesaurus, Application Domain, Technology Topic, Popular Technical Reports.
© 2025 PatSnap. All rights reserved.Legal|Privacy policy|Modern Slavery Act Transparency Statement|Sitemap|About US| Contact US: help@patsnap.com