Vacuum thermal insulation plate core material, vacuum thermal insulation plate and preparation method of vacuum thermal insulation plate
A vacuum insulation panel and core material technology, applied in the field of material science, can solve the problems of high production cost of inorganic materials such as glass fiber, high cost of inorganic materials, and burden, so as to alleviate the serious problems of environmental pollution and energy shortage, reduce glass Effect of fiber usage and cost reduction
- Summary
- Abstract
- Description
- Claims
- Application Information
AI Technical Summary
Problems solved by technology
Method used
Image
Examples
Embodiment 1
[0030] 1) Preparation of bamboo fiber pulp: at room temperature, weigh 360g of dry bamboo bleached pulp, put it in a 10L container, then add 5L of tap water, soak for 4h, and finally add it to the Valli beater, then add 18L of water Finally, start beating, and obtain the bamboo bleaching pulp that beating degree is 14.9 ° SR.
[0031] 2) Preparation of glass fiber slurry: Weigh 6.28g of glass fiber, put it in the container of the fiber dissociator, add 2300ml of water, then add 1.2g of sodium hexametaphosphate, use dilute sulfuric acid to adjust the pH of the solution to 3, and then set the defrosting switch The speed is 5000r / min, the time is 10min, and finally the dispersed glass fiber slurry is obtained.
[0032] 3) core material molding: respectively weigh two kinds of slurry according to the mass ratio of glass fiber pulp / bamboo fiber pulp 1:9, and evenly mix bamboo fiber pulp and glass fiber pulp, adopt wet papermaking technology to carry out papermaking, obtain core Ma...
Embodiment 2
[0036] 1) Preparation of bamboo fiber pulp: at room temperature, weigh 360g of dry bamboo bleached pulp, put it in a 10L container, then add 5L of tap water, soak for 4h, and finally add it to the Valli beater, then add 18L of water Finally, start beating, and obtain the bamboo bleaching pulp that beating degree is 14.9 ° SR.
[0037] 2) Preparation of glass fiber slurry: Weigh 6.28g of glass fiber, put it in the container of the fiber dissociator, add 2300ml of water, then add 1.2g of sodium hexametaphosphate, use dilute sulfuric acid to adjust the pH of the solution to 3, and then set the defrosting switch The speed is 5000r / min, the time is 10min, and finally the dispersed glass fiber slurry is obtained.
[0038] 3) core material molding: respectively weigh two kinds of pulp according to the mass ratio of glass fiber pulp / bamboo fiber pulp of 1:4, and evenly mix bamboo fiber pulp and glass fiber pulp, and use wet papermaking technology to carry out papermaking to obtain cor...
Embodiment 3
[0042] 1) Preparation of bamboo fiber pulp: at room temperature, weigh 360g of dry bamboo bleached pulp, put it in a 10L container, then add 5L of tap water, soak for 4h, and finally add it to the Valli beater, then add 18L of water Finally, start beating, and obtain the bamboo bleaching pulp that beating degree is 14.9 ° SR.
[0043] 2) Preparation of glass fiber slurry: Weigh 6.28g of glass fiber, put it in the container of the fiber dissociator, add 2300ml of water, then add 1.2g of sodium hexametaphosphate, use dilute sulfuric acid to adjust the pH of the solution to 3, and then set the defrosting switch The speed is 5000r / min, the time is 10min, and finally the dispersed glass fiber slurry is obtained.
[0044] 3) core material forming: respectively weigh two kinds of slurry according to the mass ratio of glass fiber pulp / bamboo fiber pulp 3:7, and evenly mix bamboo fiber pulp and glass fiber pulp, adopt wet papermaking technology to carry out papermaking, obtain core Ma...
PUM
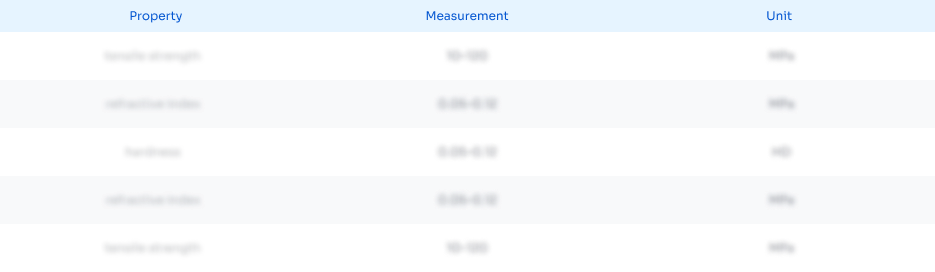
Abstract
Description
Claims
Application Information

- R&D Engineer
- R&D Manager
- IP Professional
- Industry Leading Data Capabilities
- Powerful AI technology
- Patent DNA Extraction
Browse by: Latest US Patents, China's latest patents, Technical Efficacy Thesaurus, Application Domain, Technology Topic, Popular Technical Reports.
© 2024 PatSnap. All rights reserved.Legal|Privacy policy|Modern Slavery Act Transparency Statement|Sitemap|About US| Contact US: help@patsnap.com