A target vacuum diffusion welding system and method
A technology of vacuum diffusion and welding system, applied in welding equipment, non-electric welding equipment, metal processing equipment, etc., can solve the problem of difficult welding of target and flange materials
- Summary
- Abstract
- Description
- Claims
- Application Information
AI Technical Summary
Problems solved by technology
Method used
Image
Examples
Embodiment 1
[0033] like Figure 1 to Figure 4 As shown, this embodiment provides a target 2 vacuum diffusion welding system, which includes: a target 2, a flange 1, and a force applying member; the outer peripheral surface of the target 2 is provided with a groove portion 21, and the method The side edge of the flange 1 is provided with a raised portion 11, the flange 1 is assembled on the target 2, and the raised portion 11 is set corresponding to the groove portion 21 to ensure that the raised portion 11 fits in the groove portion 21 when deformed. Of course, the raised portion 11 matches the shape of the groove portion 21 . The biasing member is used to apply stress to the raised portion 11 so that the raised portion 11 fits into the groove portion 21 . The flange 1 is extruded into the target 2 by extrusion on a lathe, and this extrusion assembly method can solve the technical problem of difficult welding of the target 2 with a special shape and the material of the flange 1 .
[00...
Embodiment 2
[0050] like Figure 1 to Figure 4 As shown, the second embodiment also provides a target 2 vacuum diffusion welding method, the target 2 vacuum diffusion welding method is carried out according to the target 2 vacuum diffusion welding system. Of course, the second embodiment includes the technical content disclosed in the first embodiment, and the same technical content as the first embodiment will not be repeated here.
[0051] The target material 2 vacuum diffusion welding method comprises the following steps:
[0052] S1. Assemble the flange 1 on the target 2, and fix the assembled target 2 in the lathe through the inner support fixture; of course, when targeting the pot-shaped target 2, only need to assemble the flange 1 on the pot-shaped For the target material 2, when targeting other shapes of the target material 2, the corresponding operation is sufficient.
[0053] S2. Stress is applied to the raised portion 11 of the flange 1 by means of a force-applying member to d...
PUM
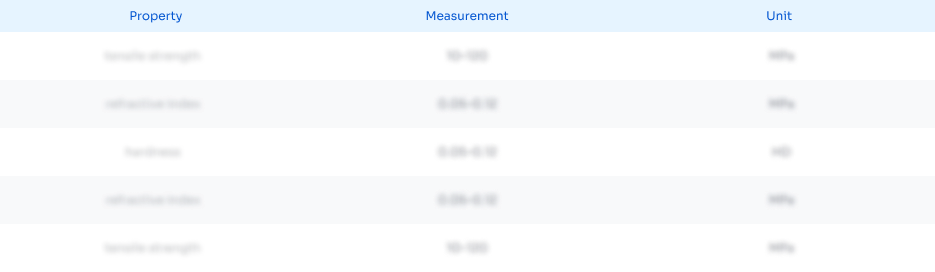
Abstract
Description
Claims
Application Information

- R&D Engineer
- R&D Manager
- IP Professional
- Industry Leading Data Capabilities
- Powerful AI technology
- Patent DNA Extraction
Browse by: Latest US Patents, China's latest patents, Technical Efficacy Thesaurus, Application Domain, Technology Topic, Popular Technical Reports.
© 2024 PatSnap. All rights reserved.Legal|Privacy policy|Modern Slavery Act Transparency Statement|Sitemap|About US| Contact US: help@patsnap.com