Method for producing clean diesel oil through coal tar hydrogenation, and system for method
A technology for coal tar and diesel oil, which is applied in the fields of hydrogenation treatment process, petroleum industry, and hydrocarbon oil treatment. It can solve the problems of instability, long-term stable operation and blockage of the slurry bed hydrogenation device, and achieve good product quality. , realize clean and efficient utilization, and improve the effect of liquid yield
- Summary
- Abstract
- Description
- Claims
- Application Information
AI Technical Summary
Problems solved by technology
Method used
Image
Examples
Embodiment 1
[0116] Based on the total weight of the coal tar raw material, the dosage of the slurry bed catalyst is 1.5% by weight based on the active metal elements contained therein. After mixing the coal tar raw material in Table 1 with the aforementioned highly dispersed heterogeneous slurry bed catalyst, they enter the slurry bed hydrogenation reactor together with hydrogen for gentle hydrogenation treatment, and the outflow of the slurry bed hydrogenation reactor The product enters the first separation unit for gas-liquid separation, and separates water, and the separated liquid hydrocarbon product enters the first fractionation tower, and is distilled and cut into light distillate, middle distillate and heavy distillate. Wherein the first fractionation tower distills and cuts 7.5% by weight of the heavy fraction out of the device; the remaining heavy fraction is circulated back to the slurry bed hydrogenation reactor for further conversion.
[0117] The raw material of anthracene o...
Embodiment 2
[0122] Present embodiment adopts the similar processing route with embodiment 1 to carry out, and what is not used is:
[0123] In embodiment 2, based on the total weight of coal tar raw material, the consumption of slurry bed catalyst is 2.0% by weight in terms of the active metal elements contained therein; the heavy fraction of 10% by weight cut out by the first separation unit out device to control the solid content in the slurry bed reactor and maintain the activity of the catalyst in the slurry bed reactor is stable, and the rest of the heavy fractions are recycled back to the slurry bed hydrogenation reactor for further conversion; the weight of the anthracene oil raw material is related to the The ratio of the weight sum of the light distillate and the middle distillate is 0.25:1; the first diesel fraction recycled back to the slurry bed hydrogenation reactor accounts for the first diesel fraction cut out by distillation in the second separation unit 35% of the total w...
Embodiment 3
[0128] Present embodiment adopts the similar processing route with embodiment 1 to carry out, and what is not used is:
[0129] In embodiment 3, based on the total weight of coal tar raw material, the consumption of slurry bed catalyst is 1.0% by weight in terms of active metal elements contained therein; the heavy fraction of 5% by weight cut out by the first separation unit out device to control the solid content in the slurry bed reactor and maintain the activity of the catalyst in the slurry bed reactor is stable, and the rest of the heavy fractions are recycled back to the slurry bed hydrogenation reactor for further conversion; the weight of the anthracene oil raw material is related to the The ratio of the weight sum of the light distillate and the middle distillate is 0.15:1; the first diesel fraction recycled back to the slurry bed hydrogenation reactor accounts for the first diesel fraction cut out by distillation in the second separation unit 25% of the total weight...
PUM
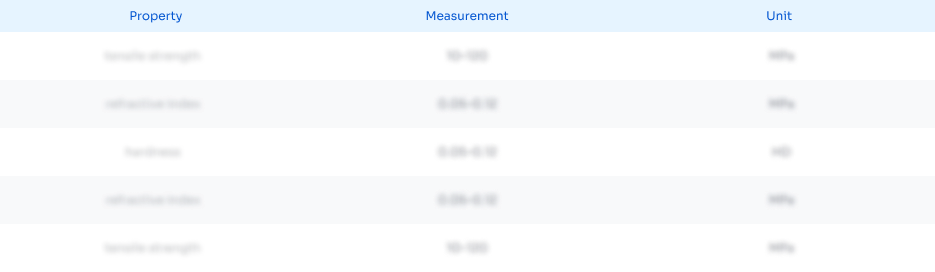
Abstract
Description
Claims
Application Information

- Generate Ideas
- Intellectual Property
- Life Sciences
- Materials
- Tech Scout
- Unparalleled Data Quality
- Higher Quality Content
- 60% Fewer Hallucinations
Browse by: Latest US Patents, China's latest patents, Technical Efficacy Thesaurus, Application Domain, Technology Topic, Popular Technical Reports.
© 2025 PatSnap. All rights reserved.Legal|Privacy policy|Modern Slavery Act Transparency Statement|Sitemap|About US| Contact US: help@patsnap.com