Once-moulded thin-tire ceramic and preparation technology thereof
A preparation process and green body technology, applied in the field of one-time molding thin-bodied porcelain and its preparation, can solve the problems of cumbersome steps, easy deformation and cracking, low output of thin-bodied porcelain, etc., achieve simple process, reduce time cost, reduce The effect of production costs
- Summary
- Abstract
- Description
- Claims
- Application Information
AI Technical Summary
Problems solved by technology
Method used
Examples
preparation example Construction
[0030] The preparation technology of the one-time molded thin body porcelain comprises the following steps:
[0031] (1), calcining albite, red stone, and quartz powder at 500-600°C for 3-4 hours, mixing and crushing with other raw materials after cooling, and passing through a 120-150 mesh sieve to obtain powder;
[0032] (2), the prepared powder was carried out wet ball milling for 48 hours to obtain mud, wherein material: ball: water=1:1.8-2.6:1.2-1.6;
[0033] (3), after the raw material of glaze is weighed according to its proportioning, break through crusher, after sieving, wet ball milling makes glaze;
[0034] (4), degassing the ball-milled mud to remove air bubbles in the mud, and stale at 45-50°C for 25-30 days to obtain mud;
[0035] (5) After the mud is spray-dried, a green body with a thickness of 0.4-0.6mm is made;
[0036] (6), apply glaze on the body, the thickness of the glaze layer is 0.08-0.12mm, wherein, the glaze method of glaze is dipping;
[0037] (7)...
Embodiment 1
[0039] The green body includes the following raw materials in parts by weight: 16 parts of albite, 18 parts of montmorillonite, 46 parts of quartz powder, 12 parts of rutile, 3 parts of molybdenum ore powder, 3 parts of silica brick powder, 5 parts of diopside, magnesium oxide 6 parts, 1 part of light calcium carbonate, Dy 2 o 3 2 parts, GeO 2 2 parts, SiO 2 1 copy;
[0040] The glaze includes the following raw materials in parts by weight: 15 parts of albite, 16 parts of red stone, 46 parts of quartz, 5 parts of titanium dioxide, 6 parts of glass powder, 3 parts of red jade, 3 parts of bentonite, 2 parts of calcium nitride, oxide Dysprosium 3 parts, carbonic acid 1 part.
[0041] Its preparation process comprises the following steps:
[0042] (1), calcining albite, red stone, and quartz powder at 562°C for 3.4 hours, mixing and crushing with other raw materials after cooling, and passing through a 150-mesh sieve to obtain powder;
[0043] (2), the prepared powder was ca...
Embodiment 2
[0050] The green body includes the following raw materials in parts by weight: 22 parts of albite, 12 parts of montmorillonite, 52 parts of quartz powder, 8 parts of rutile, 5 parts of molybdenum ore powder, 1 part of silica brick powder, 8 parts of diopside, magnesium oxide 3 parts, 3 parts of light calcium carbonate, V 2 o 5 0.35 parts, CaF 2 0.55 parts, Al 2 o 3 0.1 copies;
[0051] The glaze includes the following raw materials in parts by weight: 10 parts of albite, 22 parts of red stone, 35 parts of quartz, 8 parts of titanium dioxide, 3 parts of glass powder, 5 parts of red jade, 1 part of bentonite, 5 parts of calcium nitride, oxide Dysprosium 1 part, carbonic acid 2 parts.
[0052] Its preparation process comprises the following steps:
[0053] (1), calcining albite, red stone, and quartz powder at 600°C for 4 hours, mixing and crushing with other raw materials after cooling, and passing through a 120-mesh sieve to obtain powder;
[0054] (2), the prepared powd...
PUM
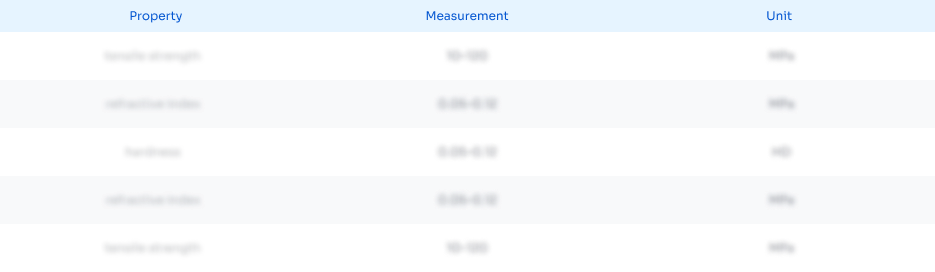
Abstract
Description
Claims
Application Information

- R&D Engineer
- R&D Manager
- IP Professional
- Industry Leading Data Capabilities
- Powerful AI technology
- Patent DNA Extraction
Browse by: Latest US Patents, China's latest patents, Technical Efficacy Thesaurus, Application Domain, Technology Topic, Popular Technical Reports.
© 2024 PatSnap. All rights reserved.Legal|Privacy policy|Modern Slavery Act Transparency Statement|Sitemap|About US| Contact US: help@patsnap.com