A kind of process of preparing zinc sulfate co-production ammonium chloride with high chloride zinc slag
A technology of ammonium chloride and zinc sulfate, applied in the direction of zinc sulfate, ammonium halide, process efficiency improvement, etc., can solve the problems of increased operating costs, large consumption of sulfuric acid, environmental pollution, etc., to achieve increased leaching rate, improved purity, The effect of achieving zero emissions
- Summary
- Abstract
- Description
- Claims
- Application Information
AI Technical Summary
Problems solved by technology
Method used
Examples
preparation example Construction
[0023] (4) Preparation of ammonium chloride: first use hydrochloric acid to adjust the pH value of the chlorine-containing liquid after step (3) to 4.5 to 7.5, then add an ion masking agent to the solution, and finally distill under reduced pressure, condense, and crystallize , to obtain the ammonium chloride product; wherein, the ion masking agent is added to 0.5-3L per cubic meter of the purified chlorine-containing liquid;
[0024] (5) Purification of the zinc dipping solution: add the purification slag produced in the step (3) to the zinc dipping solution produced in the step (2), and dissolve to obtain the zinc-containing solution, then use zinc powder as a pH regulator to adjust the zinc-containing solution solution, adjust the pH value of the zinc-containing solution to 5.0-6.5, filter to obtain filter residue and zinc-containing purification solution, then add ion masking agent to the zinc-containing purification solution, and finally undergo vacuum distillation, conden...
Embodiment 1
[0026] Embodiment 1, comprises the following steps:
[0027] (1) Water washing-ammoniation two-stage leaching of chlorine in high-chloride zinc slag: at a water washing temperature of 90°C, add high-chloride zinc slag with an average particle size of 200 μm to the water at a liquid-to-solid weight ratio of 2:1 , after washing with water for 3 hours, filter to obtain washing solution and washing slag, wherein about 85% chlorine and about 15% zinc in the high-chloride zinc slag enter the washing solution; Proportion: Add water washing slag into water, then pass through ammonia gas, adjust the pH value of the reaction system to 9.5, react for 3 hours, and filter to obtain ammonia leaching solution and ammonia leaching residue. Among them, the leaching rate of chlorine is about 89%, and the leaching rate of zinc is about 89%. The rate is 0;
[0028] After the two-stage leaching process of water washing and ammoniation, the leaching rate of chlorine is over 98%, and the leaching r...
Embodiment 2
[0034] Embodiment 2, comprises the following steps:
[0035] (1) Water washing-ammoniation two-stage leaching of chlorine in high-chloride zinc slag: at a water washing temperature of 20°C, add high-chloride zinc slag with an average particle size of 40 μm to the water at a liquid-to-solid weight ratio of 8:1 , after washing with water for 0.5h, filter to obtain washing solution and washing slag, wherein about 85% of chlorine and about 15% of zinc in the high-chloride zinc slag enter the washing solution; at 20°C, the liquid-solid weight ratio is 8:1 The proportion of water washing slag was added to water, and then ammonia gas was introduced, and the pH value of the reaction system was adjusted to 8.5. After 2 hours of reaction, it was filtered to obtain ammonia leaching solution and ammonia leaching residue. Among them, the leaching rate of chlorine was about 89%, and the leaching rate of zinc was about 89%. The leaching rate is 0;
[0036] After the two-stage leaching proce...
PUM
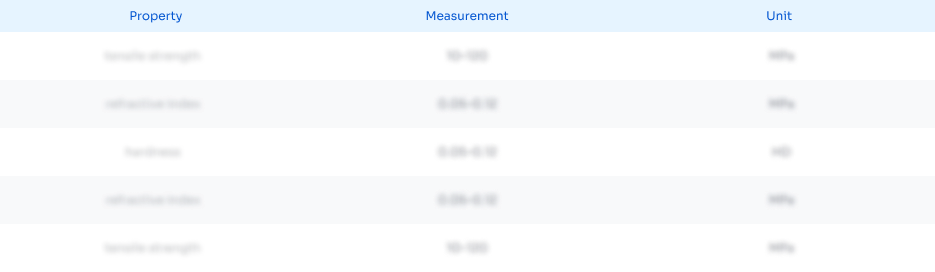
Abstract
Description
Claims
Application Information

- R&D
- Intellectual Property
- Life Sciences
- Materials
- Tech Scout
- Unparalleled Data Quality
- Higher Quality Content
- 60% Fewer Hallucinations
Browse by: Latest US Patents, China's latest patents, Technical Efficacy Thesaurus, Application Domain, Technology Topic, Popular Technical Reports.
© 2025 PatSnap. All rights reserved.Legal|Privacy policy|Modern Slavery Act Transparency Statement|Sitemap|About US| Contact US: help@patsnap.com