Production method of mixed casting of different steel types for continuous casting big round billet
A production method and a technology of different steel types, which are applied in the field of mixed casting of different steel types in continuous casting large round billets, can solve the problems of affecting the production rhythm of steel plants, difficulty in ensuring product quality, and difficulty in production organization, so as to reduce thermal shutdown time, The effect of increasing the billet rate of continuous casting billet and reducing the scrapped length
- Summary
- Abstract
- Description
- Claims
- Application Information
AI Technical Summary
Problems solved by technology
Method used
Image
Examples
Embodiment 1
[0031] Take the production of two steel grades with a carbon content difference of 0.03% and a manganese content difference of 0.02% in a Φ380 mm section of a continuous casting machine as an example.
[0032] There was still 20t of molten steel remaining in ladle 1-1 of the previous heat, and the casting speed was reduced to 0.48 m / min. After pouring the molten steel from the previous heat ladle 1-1, rotate the subsequent heat ladle 1-2 to the casting position; the liquid steel level of the previous heat ladle 1-1 in the middle ladle 2 is lowered to 380mm At the time of pouring, the ladle 1-2 of the last heat was poured, and the ladle covering agent of the tundish 2 was replaced with an ultra-low carbon ladle covering agent; the molten steel of the ladle 1-2 of the last heat When pouring is started, the casting slab that comes out of the crystallizer 4 starts to be marked at this moment, and is cut into a mixed casting slab 8 according to a fixed length; after the last batch ...
Embodiment 2
[0035] Two steel grades with a manganese content difference of 0.4% are produced on a Φ600 mm section of a continuous casting machine as an example.
[0036] The control method of the mixed casting production process is basically the same as that of Example 1, the difference is that there is still 15 tons of molten steel left in the previous batch of ladle 1-1, and the casting speed is initially reduced to 0.30 m / min;
[0037] When the remaining steel liquid level of the previous heat ladle 1-1 in the tundish 2 drops to 350mm, the latter heat ladle 1-2 starts pouring;
[0038] After casting 25t of ladle 1-2 in the next furnace, keep the molten steel level in tundish 2 at 500mm~700mm, and increase the casting speed to the maximum casting speed allowed by the process of 0.36m / min;
[0039] After the pouring of ladle 1-2 in the last heat, when casting in tundish 2 for 10 minutes, replace the mold slag of mold 4 from manganese steel mold slag to medium carbon steel mold slag.
[...
PUM
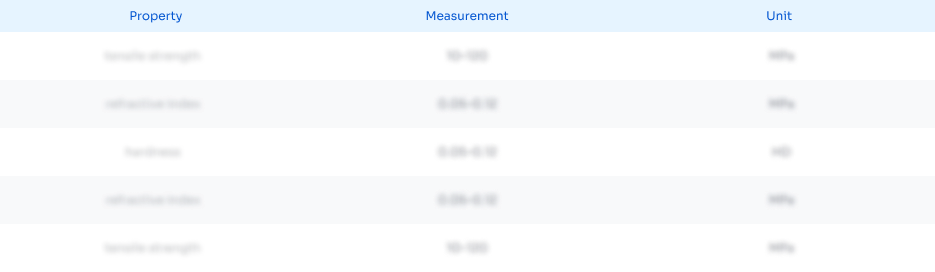
Abstract
Description
Claims
Application Information

- R&D
- Intellectual Property
- Life Sciences
- Materials
- Tech Scout
- Unparalleled Data Quality
- Higher Quality Content
- 60% Fewer Hallucinations
Browse by: Latest US Patents, China's latest patents, Technical Efficacy Thesaurus, Application Domain, Technology Topic, Popular Technical Reports.
© 2025 PatSnap. All rights reserved.Legal|Privacy policy|Modern Slavery Act Transparency Statement|Sitemap|About US| Contact US: help@patsnap.com